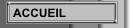
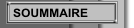
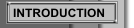
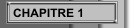
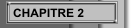
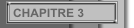
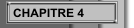
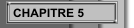
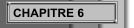
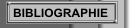
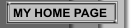
|
CHAPITRE 3
LE COMPORTEMENT DES ACIERS INOX A LA CORROSION ET A L’USURE
La corrosion [100] est une interaction
physico-chimique entre un
métal
et son milieu environnant entraînant des modifications dans les
propriétés du métal et souvent une dégradation fonctionnelle du métal
lui-même, de son environnement ou du système technique constitué par
les deux facteurs.
NOTE - Cette interaction est
généralement de nature
électrochimique.
On voit donc que le litige est de savoir
si la corrosion est le
processus lui-même, ou le résultat, ou l’ensemble. C’est la première
notion qui a été retenue: la corrosion est le processus lui-même, son
résultat étant une attaque, un dégât dû à la corrosion.
La corrosion est donc un processus de
dégradation des métaux qui, à
l'exception des métaux précieux tels que l'or, ont toujours tendance à
s'altérer au contact de l'atmosphère, des eaux et des divers milieux
corrosifs. On estime, que chaque année, le quart de la production
d'acier est détruite par la corrosion. Cette corrosion qui apparaît
soit en milieu sec, soit en milieu humide, a de tels effets que
l'utilisation des aciers inoxydables constitue la solution idéale pour
la prévenir.
La norme ISO 8044 regroupe l’ensemble
des définitions concernant les
mécanismes de corrosion, notamment en fonction des milieux considérés :
corrosion gazeuse, corrosion atmosphérique, etc.
On utilise l'acier inoxydable pour
solutionner tous les problèmes de
corrosion dans les milieux ambiants corrosifs (chimie, nucléaire,
chantiers navals, plaisance, bâtiment, traitement des eaux,
agro-alimentaire, mobilier urbain, électronique). En effet, l'acier
inoxydable est résistant à la corrosion en milieux aqueux en présence
de nombreux agents agressifs, organiques et minéraux. De plus, cet
acier résiste à la corrosion à haute température en milieux gazeux et
visqueux. Cette résistance à la corrosion est due à la présence de
chrome (au moins 12%). Cet élément forme à la surface de l'alliage un
composé oxydé qui a la propriété d'arrêter ou de ralentir la corrosion
(couche passive). La stabilité de la couche passive est le facteur
déterminant de la résistance à la corrosion des aciers inoxydables.
Elle dépend de la nature des éléments d'alliage qui constituent
l'acier, de l'état de surface, du traitement de passivation préalable.
LA RESISTANCE A LA CORROSION DES ACIERS
INOXYDABLES
L’aciers inoxydables se sont pas
infaillibles vis-à-vis de la
corrosion. Les types de corrosion des aciers inoxydables alimentaires
sont (tableau 3.1):
- La corrosion généralisée;
- La corrosion localisée.
Du fait de la résistance intrinsèque de
l'acier inoxydable, la
corrosion généralisée, c'est-à-dire l'attaque de toute la surface, est
un incident rare dans l'agroalimentaire; elle se produit uniquement
dans le cas de milieux très acides. Le seul remède est alors de changer
de nuance d'acier au stade de la conception de l'équipement ou de
considérer l'acier inoxydable comme un matériau consommable.
Par opposition à la corrosion uniforme,
la corrosion localisée (plus
spécifique pour les aciers inoxydables), intervient sur des sites
discrets de la surface d'un métal exposé à un environnement corrosif.
NOTE - La corrosion localisée peut, par
exemple, apparaître sous forme
de piqûres, fissures, sillons, etc.
On a souvent dit que la corrosion
localisée était une «maladie de
l'état passif».
D'une façon plus générale, on peut dire
qu'une corrosion localisée
intervient chaque fois qu'il existe, dans le système de corrosion
considéré, une hétérogénéité:
- soit du métal,
- soit du milieu,
- soit des conditions physico-chimiques
existant à l'interface.
La première approche de la corrosion
étant généralement visuelle, on
distingue traditionnellement les corrosions localisées, soit par la
forme de l'attaque qui en résulte (corrosion par piqûres), soit par la
localisation (par ex. corrosion intergranulaire). Dans d'autres cas
cependant, la désignation est associée à un mécanisme (corrosion par
effet de crevasse, corrosion sous contrainte, corrosion-érosion).
LES FORMES DE CORROSION LOCALISEE
SPECIFIQUE AUX ACIERS INOXYDABLES
ALIMENTAIRES
LA CORROSION PAR PIQURES
La corrosion par piqûres est fréquente
et pernicieuse. Elle est surtout
le fait des halogènures: chlorures, fluorures, etc. C'est un risque
important en agroalimentaire, car les chlorures sont souvent présents
dans le procédé (saumures) ou dans les produits de nettoyage ou de
désinfection (eau de Javel) [2].
La corrosion par piqûres est
dommageable, car les cavités créées facilitent l'accrochage des
salissures.
La corrosion par piqûres (pitting) est une forme de corrosion localisée
au cours de laquelle le métal se dissout très rapidement en certains
sites discrets de la surface, le reste de cette surface n'étant
sensiblement pas attaqué. Cela se traduit souvent par la formation de
trous de faibles dimensions mais de profondeur importante. La
conséquence d'une telle attaque peut être la destruction rapide et
inattendue des structures sur lesquelles elle se manifeste. La
corrosion par piqûres est d'autant plus insidieuse qu'elle se produit
sur des matériaux passivables, présentant donc une excellente
résistance à la corrosion généralisée.
La plupart des matériaux sont sensibles
à la corrosion par piqûres mais
la présence d'espèces agressives spécifiques est nécessaire. Ce sont le
plus souvent les ions halogénures dont l'agressivité se manifeste
vis-à-vis de la grande majorité des matériaux. Parmi ceux-ci, les
chlorures revêtent une importance particulière en raison d'une part, de
leur grande distribution dans la nature et, d'autre part, de leur
agressivité généralement plus élevée que celles des bromures et des
iodures bien que le contraire ait été parfois observé comme, par
exemple, pour les aciers inoxydables au molybdène [3]. D'autres espèces
soufrées (H2S pour les aciers inoxydables) peuvent toutefois provoquer
l'apparition de piqûres [9].
Remarquons que les ions nitrates sont
réputés pour leurs propriétés
inhibitrices de la corrosion par piqûres de nombreux matériaux : fer et
aciers au carbone [11], aciers inoxydables [12], nickel [11], zirconium
[13] et aussi aluminium [41].
La présence d'anions agressifs n'est pas
une condition suffisante pour
que la corrosion par piqûres se manifeste. En effet, pour tous les
métaux, il existe une concentration limite en ions agressifs en dessous
de laquelle la corrosion par piqûres ne se développe pas. La valeur de
cette concentration limite est fonction de la composition de
l'électrolyte.
LA CORROSION CAVERNEUSE
La corrosion caverneuse est un phénomène de
corrosion localisée qui se
développe dans des interstices, des zones de recoin où un matériau
métallique se trouve localement en contact avec un milieu corrosif
confiné, alors que la majorité de la surface du matériau est au contact
de la masse du liquide.
En pratique la présence de zones confinées provient de différentes
origines
la conception des appareillages (figure 3.1)
- la formation de dépôts, soit en
service, soit même pendant la
fabrication
- dépôts minéraux ou organiques dans
des zones de relative stagnation
- produits de corrosion
- développements biologiques.
De façon très générale, la corrosion
caverneuse est due à une
modification locale du milieu, ce qui, entraîne un changement des
conditions électrochimiques dans la caverne [1-6]. Il s'ensuit
l'apparition de piles de concentration et d'un couplage galvanique
entre l'intérieur et l'extérieur de la caverne (figure 3.2.). En
conséquence, les vitesses de corrosion deviennent différentes et des
migrations électrolytiques se produisent entre l’intérieur et
l’extérieur de la caverne. Cet ensemble de processus est très souvent
auto-accéléré par les différences de conditions électrochimiques entre
l’intérieur et l’extérieur de la caverne.
Le plus souvent, les conditions
électrochimiques deviennent plus
sévères dans la caverne et la corrosion y devient plus rapide. C'est le
cas des phénomènes de caverne sur les matériaux passifs.
Les caractéristiques d'une caverne à
l'origine de l'évolution locale du
milieu sont résumées dans la figure 3.3.
Mécanisme de l'évolution de la solution
dans une caverne en milieu
chloruré aéré.
Stade 1
- Epuisement local de l'oxydant
insuffisamment renouvelé, par la
diffusion de l'extérieur vers l'intérieur de la caverne. Ceci vaut pour
des oxydants tels que l'oxygène de l'air, l'acide nitrique, les
chromates, ... En soi, cette disparition locale de l'oxydant ne suffit
pas à causer de corrosion localisée mais elle constitue l'étape
initiale nécessaire à l'évolution du milieu par suppression locale de
la réaction cathodique.
- Au passage, on doit remarquer qu'en
milieux chlorurés non oxydants,
la réaction cathodique est la réduction de l'eau et qu'elle reste
toujours possible dans la caverne. Ainsi, il ne peut y avoir de moteur
initial à la corrosion caverneuse, car la cause première de
l'acidification n'existe pas.
Stade 2: acidification et concentration
en chlorures (figures 3.2b et
3.2c)
- Après épuisement en oxydant,
l'ensemble des processus anodiques se
poursuit dans la caverne et conduit à la formation de cations
métalliques et d'ions H+.
- La réaction cathodique nécessaire
pour consommer les électrons
libérés par les processus anodiques ne peut se produire que sur les
surfaces extérieures à la caverne. Elle ne peut donc neutraliser
localement les ions H+ produits par les processus anodiques.
- La neutralité électrique des
solutions est maintenue par
l'établissement d'une migration électrolytique: cations de l'intérieur
vers l'extérieur de la caverne, ce qui évacue une partie des cations
métalliques et des ions H+ produits par les processus anodiques, et
anions de l'extérieur vers l'intérieur de la caverne, ce qui y
introduit un surplus de chlorures.
- La migration électrolytique des ions
à travers une solution dont la
résistance est non négligeable, notamment du fait de la géométrie des
cavernes, conduit à l'apparition de gradients de potentiel
électrochimique non seulement entre l'intérieur et l'extérieur de la
caverne mais aussi à l'intérieur de la caverne.
En résumé, le milieu dans la caverne se
concentre progressivement en
cations métalliques plus ou moins hydrolysés, en chlorures, et en ions
H+ et devient donc de plus en plus acide. Corrélativement,. les flux
migratoires augmentent entre l'extérieur et l'intérieur de la caverne
et la différence de potentiel augmente également. Il faut aussi noter
que le pH augmente légèrement autour de la caverne, sur l'ensemble de
la zone sur laquelle est distribué, l'excès de réaction cathodique.
L'étendue de cette zone dépend de la résistivité du milieu chloruré, et
de la cinétique des réactions dans la caverne. Quand la caverne est le
siège d'une corrosion active, cette zone cathodique est souvent le
siège d'une précipitation d'hydroxydes, ce qui crée une sorte d'auréole
autour des cavernes (ou des piqûres) actives.
Moyens de prévention et de lutte contre
la corrosion caverneuse.
Ils interviennent à différents stades:
- conception
des appareillages: il s'agit d'abord de minimiser les
zones de caverne existant lors de la mise en service et ceci relève de
la conception des ensembles: on peut par exemple éviter des soudures
avec recouvrement, remplacer des brides à joints par des assemblages
soudés, sertir (dudgeonner) les tubes dans les plaques tubulaires
d'échangeurs, polir des portées de joints et, de façon générale, éviter
les interstices de toute nature. Mais il faut parfois aussi penser à
minimiser les risques de formation de caverne au cours du
fonctionnement de l'appareillage ; par exemple des conditions
hydrodynamiques bien étudiées peuvent éviter la formation de dépôts.
- mise
en oeuvre des matériaux: une mise en oeuvre soignée permet
d'éviter de dégrader localement les propriétés des matériaux utilisés:
une attention particulière doit donc être portée aux procédures de
soudage, aux éventuels traitements thermiques et à l'état de surface
(micro-géométrie, pollutions, composition superficielle). Une mise en
propreté finale par décapage et passivation ne peut qu'être bénéfique
dans le cas des aciers inoxydables.
- conduite
des installations: des procédures appropriées, notamment en
périodes transitoires ou même pendant les périodes d'arrêt, peuvent
être d'une grande importance pour conserver l'intégrité de certaines
installations. Par exemple, on a déjà mentionné précédemment le cas des
précautions à prendre sur des installations de dessalement de l'eau de
mer pour éviter les entrées d'air pendant les périodes d'arrêt. Le
maintien de la propreté des installations et l'élimination périodique
de dépôts en formation peuvent aussi constituer une action efficace
contre la corrosion caverneuse.
- choix
des matériaux: le choix de matériaux résistant à la corrosion
caverneuse est évidemment nécessaire, mais le coût d'une installation
peut augmenter considérablement si des aciers inoxydables très alliés,
des alliages à base nickel ou des alliages de titane sont utilisés. Or,
le degré de résistance demandé au matériau peut dépendre de façon
significative de la conception de l'appareillage, de la mise en oeuvre
(soudage en particulier) et/ou des procédures d'exploitation. Le choix
d'un matériau très résistant ne doit donc pas nécessairement être
considéré comme la seule solution au problème de caverne, et il doit
prendre en compte non seulement les conditions de fonctionnement
nominales, mais aussi les périodes transitoires et les excursions
possibles hors des conditions nominales.
- protection
électrochimique: enfin, il est également possible de
protéger des installations contre la corrosion caverneuse en maintenant
leur potentiel dans des zones de potentiel appropriées. Dans le cas des
aciers inoxydables, il s'agit de maintenir le potentiel en deçà du
potentiel de protection, au moins dans certaines zones critiques. Ceci
peut être obtenu du fait de couplages avec des matériaux moins nobles
présents dans l'installation, par l'utilisation d'anodes sacrificielles
ou par application de courants. C'est par exemple la protection
cathodique des aciers inoxydables martensitiques de type Z5 CND 17-4.
CORROSION INTERGRANULAIRE
CORROSION INTERGRANULAIRE HORS
PRECIPITATION (CIGHP)
La corrosion intergranulaire hors
précipitation est observée dans des
solutions oxydantes: il se produit une dissolution sélective localisée
à l'émergence de certain ou de tous les joints de grains sur la
surface. Cette corrosion peut amener à un déchaussement des grains et à
la destruction catastrophique du métal (figure 3.4).
Ces conditions de corrosion
intergranulaire sont susceptibles d'être
reproduites et étudiées en laboratoire. Cependant, d'autres tests
chimiques et électrochimiques ont été mis au point pour étudier
différents paramètres corrélant les aspects structuraux et chimiques
des joints de grains et des interphases.
Facteurs de la corrosion
intergranulaire (CIGHP).
Les phénomènes de corrosion localisée
sont le plus souvent liés à des
imperfections structurales et/ou chimiques des matériaux. Ces processus
se produisent sur les défauts de la matrice cristalline
- dislocations,
- joints de grains,
- interphases de type
austéno-ferritique.
De ce fait, on met en cause les facteurs
physico-chimiques des défauts
structuraux :
- structure atomique et composition
chimique en volume,
- ségrégation
d'impuretés,
- phase bidimensionnelle.
Il est essentiel de remarquer que la
corrosion aqueuse est un processus
qui ne concerne que la surface et pas les propriétés de volume. Il ne
faut donc considérer que la réactivité de l'émergence des joints de
grains et interphases à l'interface métal- solution.
Trois processus sont à prendre en compte:
- la création de la double couche
chimique ou électrochimique à la
surface du métal. Pratiquement dans tous les cas se forme en outre une
couche barrière : film de corrosion
- l'amorçage ou nucléation de la
corrosion intergranulaire qui est
contrôlée par le film de corrosion et par la réactivité de la structure
atomique. Par exemple, les sites actifs de dissolution et leur
distribution sont déterminés par des facteurs métallurgiques et par
l'homogénéité chimique de la surface;
- la croissance ou propagation qui
nécessite la reproductibilité de
l'étape précédente mais qui est aussi influencée par les facteurs
cinétiques tels que la formation d'un film de corrosion, la diffusion
des espèces réactives, la passivité et la polarisation.
Les facteurs de
la corrosion intergranulaire.
Schématiquement, nous sommes en présence
d'une interface
matériau-milieu comportant:
- le métal que l'on peut décrire par:
sa structure cristallographique,
sa composition chimique, les défauts de structure dont les joints de
grains ;
- la "surface" caractérisée par la
répartition des électrons, la
structure des défauts émergents (marches et coins atomiques, joints de
grains...), la réactivité chimique et électrochimique, le film de
corrosion et ses propriétés mécaniques, de diffusion chimique et de
conduction électrique, la double couche électrochimique, les propriétés
des sites de nucléation ;
- le milieu d'attaque, sa composition,
ses propriétés redox, les
composantes électrochimiques : potentiel et différentiel
cathodique-anodique.
Le tout peut se résumer par une énergie
de l'atome à la surface du
métal, une énergie de l'intermédiaire de réaction à la surface,
l'énergie d'équilibre finale en solution. C'est la différence
énergétique de ces trois états qui explique les différences de
corrosion dans les joints de grains. La nucléation de la corrosion
intergranulaire est contrôlée par la "surface". Les sites actifs de
dissolution et leur distribution sont déterminés par les facteurs
métallurgiques et l'homogénéité chimique et mécanique de la surface.
La croissance ou propagation de la
corrosion intergranulaire nécessite
la reproductibilité dans le temps de l'étape précédente. Elle est
influencée par la formation d'un film de corrosion en surface et aux
joints de grains qui fixe les facteurs cinétiques de dissolution
(polarisation, diffusion des espèces réactives, sites de nucléation).
CORROSION INTERGRANULAIRE LIEE A LA
PRECIPITATION D’UNE SECONDE PHASE
Dans de nombreux cas, la corrosion
intergranulaire (figure 3.5) est
plutot liée à la précipitation d’une (ou plusieurs) phase (s) aux
joints de grains, carbures de chrome ou composés intermétalliques par
exemple. Il résulte de cette précipitation une modification locale de
la composition ainsi que l’existence de piles électrochimiques qui
peuvent parfois impliquer plus de deux électrodes; ces piles sont en
général très actives.
Cas des aciers inoxydables austénitiques
Un acier inoxydable austénitique à l'état
sensibilisé est caractérisé
par la précipitation du carbure Cr23 C6. Ce carbure, très riche en
chrome, a appauvri la zone voisine en cet élément (figure 3.6). Le
système comporte alors trois zones distinctes qui vont donner lieu à
trois électrodes, donc à un système (Fig. 3.7):
- le carbure de chrome à un potentiel
noble donc cathodique (domaine
I)
- la zone déchromée dont la passivité
n'est plus stable et qui adopte
un potentiel anodique (domaine II)
- le coeur des grains de l'austénite
dont la teneur en chrome n'a pas
été modifiée et qui a la matrice à l'état hypertrempé (domaine III)
Il en résulte que la zone déchromée
s'attaque suivant les
caractéristiques du milieu environnant qui vont imposer le potentiel de
travail on voit de suite qu'il peut y avoir risque de corrosion
intergranulaire . Cette attaque résulte de la modification locale de
composition de l'acier.
Cas des aciers inoxydables ferritiques.
La corrosion intergranulaire des aciers
inoxydables, telle que nous
venons de la décrire, n'est pas spécifique des nuances austénitiques,
en effet d'autres nuances y sont sensibles et en particulier les aciers
ferritiques. La différence entre ces deux types d'aciers vient du fait
que les conditions thermiques provoquant la précipitation des secondes
phases aux joints de grains ne sont pas les mêmes. La diffusion du
carbone est plus rapide dans la ferrite que dans l'austénite; il en
résulte qu'une trempe à l'eau après un traitement thermique
d'homogénéisation à haute température (traitement de mise en solution
du carbone), n'est pas suffisamment énergique pour éviter toute
précipitation des carbures de chrome lors du refroidissement. Pour les
nuances ferritiques, il faut, outre le carbone, prendre aussi en compte
l'azote qui peut donner des nitrures, ce qui conduit au même effet. La
corrosion résultant de la précipitation de nitrures s'observe surtout
dans le cas des aciers à très basse teneur en carbone (< 0,010 % en
poids) ou encore dans les aciers à l'azote. La précipitation, pour des
raisons cinétiques, est la plus marquée entre 540 et 600°C. Toutefois
un traitement thermique à 800°C suffit pour rehomogénéiser la
distribution du chrome de part et d'autre du joint car le coefficient
de chrome dans la ferrite est élevé. C'est pour cette raison que les
nuances ferritiques sont considérées comme plus résistantes que les
nuances austénitiques.
Cas des aciers austéno-ferritiques.
Ces nuances offrent une bien meilleure
résistance à la corrosion
intergranulaire. Ceci tient au fait que cette structure biphasée
contient de la ferrite alpha plus riche en chrome et de l'austénite
gamma plus
riche en carbone. La précipitation de carbures, si elle intervient, a
lieu aux interfaces alpha/gamma; ceci diminue donc le taux de
précipitation par
unité d'aire de surface aux joints de grains de l'austénite (interfaces
gamma/gamma). On en déduit que la résistance à cette forme de corrosion
localisée pour ce type d'aciers va dépendre du rapport des phases
ferritique et austénitique; ce rapport dépend lui-même de la
composition chimique des aciers et des traitements thermiques (cf. le
diagramme de Schaeffler ou les diagrammes équivalents). Par ailleurs,
le chrome précipité sous forme de carbures provient de la ferrite; il
en résulte que l'appauvrissement de l'austénite est moins important
qu'en absence de phase ferritique. De façon générale, les nuances
courantes d'aciers austéno-ferritiques sont sensibilisées à la suite de
traitements thermiques à des températures comprises entre 400 et 850°C;
un recuit entre 950 et 1000°C permet d'éviter ce type d'attaque.
Cas des aciers martensitiques.
La température de traitement où la
sensibilisation est très marquée
pour ces aciers, est voisine de 500°C; toutefois, la précipitation de
carbures et de nitrures intervient dès 300°C; l'acier est sensibilisé,
dans les zones où le constituant martensitique est décomposé. Un
traitement thermique à une température supérieure à 700°C restaure la
résistance à la corrosion intergranulaire.
REMEDES POUR PREVENIR LE RISQUE DE
CORROSION INTERGRANULAIRE.
La compréhension des mécanismes de
corrosion intergranulaire des aciers
suggère plusieurs remèdes efficaces à mettre en oeuvre pour prévenir
cette forme d'attaque localisée.
- prolonger le traitement thermique de
revenu pour homogénéiser la
teneur en chrome et combler la "vallée" de concentration au voisinage
du joint où est précipité le carbure afin que la teneur de cet élément
soit supérieure en tout point à celle du seuil de passivité stable (12%
en poids). Cependant, cette solution implique des durées longues, non
réalistes en pratique. De même, la dimension trop grande de certaines
structures soudées ne permet pas la mise en oeuvre industrielle d'une
telle solution, élégante sur le plan métallurgique.
- réduire la teneur en carbone à une
valeur suffisamment faible pour ne
pas risquer une précipitation de carbures aux joints: une teneur
inférieure à 0,03% en poids se révèle satisfaisante, pour des
conditions usuelles; des nuances dites à bas carbone ont ainsi été
développées. Cependant, compte tenu du caractère fortement -gène du
carbone, il est nécessaire pour conserver la structure austénitique,
d'augmenter la teneur en nickel: l'acier Z6 CN 18-09 (AISI 304) devient
l'acier Z3 CN 18-10 (AISI 304 L); il contient 1 % en poids de nickel en
plus pour compenser l'abaissement de 0,03% en poids de carbone (ceci
illustre le caractère fortement gamma-gène du carbone par rapport à
celui du nickel). De même, l'acier au molybdène Z6 CND 17- 11 (AISI
316) devient l'acier Z3 CND 17-12 (AISI 316 L);
- ajouter des éléments dont l'affinité
pour le carbone est supérieure à
celle du chrome: titane, niobium, vanadium ou tantale: ils donnent
naissance à des carbures de type MC. Leurs teneurs dépendent de la
teneur totale CT en carbone de l'acier: on obtient alors des nuances
dites stabilisées (Z6 CNT 18-1 1, Z6 CNNb 18-1 1, dérivées de l'acier
Z6 CN 18-09, ou encore Z8 CNDT 17-12, Z6 CNDNb 17-12, dérivées de
l'acier Z6 CND 17-11);
- ajouter un élément alphagène comme le
molybdène. Après hypertrempe,
la structure obtenue comporte, au sein de la matrice austénitique, des
ilôts de ferrite. Comme indiqué ci-dessus, les solubilités du carbone
et du chrome étant respectivement plus grandes dans l'austénite et dans
la ferrite, les carbures de chrome se forment aux interfaces
austénite-ferrite. Il y a certes risque de corrosion intergranulaire,
mais celle-ci ne se fait plus de façon continue le long de tous les
joints de grains.
CORROSION SOUS CONTRAINTES
Ce type de corrosion, surtout présente
dans la structure austénitique
des aciers du même nom, est souvent initié par des piqûres. Elle se
traduit par des réseaux de fissures perpendiculaires aux contraintes de
traction. Ce phénomène trouve son origine dans le milieu d'utilisation
et se propage en fonction des conditions de service. Pour l'éviter, la
fabrication doit induire un minimum de contraintes résiduelles
EROSION - CORROSION, CAVITATION –
CORROSION ET CORROSION LOCALISEE
Dans de très nombreuses installations
industrielles, les matériaux sont
en contact avec un fluide agressif en mouvement, ce fluide pouvant
éventuellement contenir une deuxième phase solide, liquide ou gazeuse.
Aux dégradations induites par la corrosion, liées à la composition du
milieu, s'ajoutent des dommages mécaniques liés à la vitesse de
circulation du fluide (érosion -corrosion) et aux interactions
surface/particule (érosion -corrosion ou abrasion -corrosion,
cavitation -corrosion). L'analyse de tels phénomènes est complexe car
les processus de corrosion peuvent être considérablement modifiés
lorsqu'on passe de conditions statiques à des conditions dynamiques
(transport de matière) et lorsque les conditions peuvent être
localement perturbées par l'impact de particules ou de bulles.
L'ensemble des phénomènes de corrosion
induits par un fluide corrosif
en mouvement peut se classer selon deux groupes de processus:
- Les processus qui font intervenir le
transport de matière seul,
- Les processus qui résultant d'un
couplage entre un endommagement
mécanique et des processus chimiques contrôlés par le transport de
matière.
L'origine de la deuxième phase détermine la nature du phénomène (Fig.
3.8):
- Existence d'une seconde phase liquide
non miscible : mécanisme
contrôlé par le transport de phase ;
- Existence de bulles qui implosent à
la surface: mécanisme de
cavitation
- Existence de particules solides en
suspension dans l'électrolyte:
mécanisme d'érosion ou d'abrasion.
Ces phénomènes d'érosion - corrosion ou
d'abrasion - corrosion peuvent
induire des phénomènes de corrosion localisée qui peuvent être
caractérisés par la nature des cellules galvaniques induites. Trois
types de cellules galvaniques (c'est-à-dire coexistence de surfaces
anodiques et cathodiques) peuvent être induits par un écoulement mono
ou diphasique:
- Cellules galvaniques macroscopiques
(généralement stables dans le
temps);
- Cellules galvaniques microscopiques
(caractérisées par leur
existence transitoire);
- Cellules galvaniques microscopiques
induites par l'hétérogénéité du
matériau (existence de phases plus résistantes mécaniquement).
Suite aux variations de conditions
hydrodynamiques et aux
endommagements mécaniques induits par le fluide (mono ou diphasique) en
mouvement, des processus de corrosion peuvent intervenir dans des
milieux qui, en conditions statiques, ne génèrent pas ce type de
corrosion. De même, dans des milieux favorisant la corrosion localisée
en conditions statiques (milieux chlorures neutres, par exemple),
l'érosion ou la cavitation peuvent jouer un rôle favorable ou
défavorable suivant les conditions.
CORROSION GALVANIQUE
La corrosion galvanique se définit
simplement par l'effet de corrosion
résultant du contact de deux métaux ou alliages différents, immergés
dans un environnement corrosif conducteur. On utilise aussi le terme de
bimétallisme.
Lorsqu'un métal est immergé dans une
solution électrolytique
quelconque, on peut mesurer son potentiel libre de dissolution
(potentiel d'abandon ou de corrosion naturelle) à l'aide d'une
électrode de référence et d'un millivoltmètre à haute d'entrée. Dans
chaque solution, il est alors possible d'établir la série galvanique,
c'est-à-dire un classement des différents métaux et alliages selon le
potentiel expérimental mesuré. La figure 3.9 illustre, à titre
d'exemple, les séries relevées en solution de salive et en eau de mer.
Lors d'un couplage (contact ou liaison électrique externe entre deux
alliages différents, il s'établit un courant électronique entre eux,
résultant de leur différence de potentiel. On a, généralement,
accroissement de la corrosion de l'alliage le moins noble (anodique) et
diminution, voire suppression, de la corrosion de l'alliage le plus
noble (cathodique).
CORROSION SELECTIVE
Comme son nom indique, ce mode de
corrosion se définit comme la
dissolution préférentielle de l’un des éléments constituant l’alliage
s’il est homogène, ou l’une des phases de cet alliage s’il est
hétérogène.
L'attaque sélective due aux effets
galvaniques entre la phase
ferritique et la phase austénitique des aciers inoxydables duplex a été
étudiée par plusieurs auteurs [28]. Il apparaît que:
- dans les milieux fortement agressifs
ou ceux conduisant à une
acidification locale par hydrolyse des sels métalliques (sous dépôt ou
dans une zone stagnante), la phase la moins noble est la ferrite. Dans
ce cas, le matériau se trouve alors déplacé dans son domaine actif et
l'effet galvanique entre les deux phases α et γ prend de l'importance.
- à l'état passif, les risques de
corrosion sélective sont très
limités, voire inexistants.
- dans la pratique industrielle, ce
type de détérioration se rencontre
parfois associé à d'autres modes (piqûre, corrosion sous contrainte).
Selon les conditions locales, les deux phases α ou γ peuvent être
l'objet de l'attaque sélective, compte tenu de la différence de
composition, en particulier en chrome, nickel et molybdène de ces deux
phases.
Dans une étude assez complète sur des
aciers duplex Fe-Cr-10 % Ni, Yau
et Streicher [29] ont montré que, dans les acides réducteurs, la
ferrite constitue toujours la phase la moins noble. Sa vitesse de
corrosion augmente avec l'augmentation de la teneur en chrome et la
diminution de la teneur en nickel. La corrosion est aggravée par le
couplage défavorable avec la phase austénitique cathodique. Cette
aggravation dépend naturellement de la répartition des surfaces
relatives α/γ en contact avec le milieu et cet effet de rapport de
surface est d'ailleurs plus important que le gradient de composition
entre les deux phases.
Dans la figure 3.10 ont présenté
schématique les formes de corrosion
présentée au-dessus.
POUR LA RESISTANCE A LA CORROSION
- il faut connaître la composition
complète et précise des solutions
qui seront en contact avec le matériau (produit nettoyage, par exemple);
- il faut connaître la température de
ces différentes solutions
- il
faut aussi connaître les autres matériaux qui pourront être en contact
avec le produit et les méthodes de fabrication de l'ensemble si la
pièce ne représente qu'une partie d'un ensemble.
La résistance du
matériau : on devra regarder quel poids devra supporter la pièce pour
choisir la résistance de l'acier entre les trois classes de propriétés.
Pour choisir notre acier, il faut
regarder sa composition chimique et
ceci à l'aide d'une figure comme ci-dessous (figure 3.11): Figure 3.11.
Influence de la composition chimique sur la résistance à la corrosion :
En résumé, on regardera la composition
chimique de l'acier, la
propriété et le domaine d'application.
LES EXIGENCES DE LA SURFACE
La conception hygiénique des matériels
destinés à l'agroalimentaire se
fonde sur des règles de tenue à la corrosion et de nettoyabilité, avec
la contrainte supplémentaire qu'est l'alimentarité des matériaux et des
traitements de finition.
Face à la diversité des machines qu'elle
utilise, (remplisseurs,
mélangeurs, autoclaves, échangeurs, hachoirs, broyeuses, pompes, fours,
façonneuses, conditionneurs ... ) l'industrie agroalimentaire met en
œuvre la plupart des matériaux de base. L'acier inoxydable entre dans
l'ensemble des secteurs alimentaires et à tout stade de transformation
des aliments.
Ces matériaux ne répondent pas toujours
à l'ensemble des sollicitations
auxquelles ils sont soumis. Ils peuvent subir généralement différents
traitements de surface. Dans les zones alimentaires, il n'est pas rare
d'appliquer un revêtement sur un substrat relativement noble tel que
l'acier inoxydable afin de garantir les propriétés anticorrosion du
matériel dans son ensemble. Quel que soit le but du traitement (usure,
fatigue superficielle ... ) la surface doit de toute façon résister à
la corrosion, être exempte d'oxydes et son état doit être contrôlé afin
d'éviter les sites d'accrochage des souillures. Il faut également
s'assurer de l'adhérence des revêtements dont la porosité doit être
nulle et la fissuration, limitée.
Deux zones aux exigences différentes
Une construction pour l'agroalimentaire
est d'après la directive «
Machines » constituée de deux zones, l'une en contact avec les denrées
alimentaires et l'autre où ce contact n'existe pas. La zone alimentaire
comprend toute surface des machines, appareils ou équipements avec
laquelle les denrées alimentaires viennent en contact dans les
conditions normales d'utilisation ou accidentellement si elles peuvent
sans intervention retourner dans la masse des produits traités.
Au niveau européen, au-delà de la
directive «Machines», des exigences
sur les surfaces peuvent être précisées dans des normes générales de
conception hygiénique ou dans des normes spécifiques à un type
d'équipement (trancheurs, façonneuses, coupe - légumes, batteurs -
mélangeurs). Bien souvent des publications d'organismes font références
et servent de base aux travaux normatifs: EHEDG (européen), Campden
(anglais), FIL (industrie laitière), 3A (américain).
En fonction des zones considérées, les
contraintes en corrosion et
traitement de surface sont différentes. Dans la zone alimentaire, les
surfaces des matériaux et revêtements doivent être résistantes à la
corrosion vis-à-vis des aliments et des produits de nettoyage, non
absorbantes, durables, nettoyables, si nécessaire désinfectables, sans
cassure, résistantes aux craquelures, au fissurage, à l'écaillage, à
l'abrasion. Avec souvent un état de surface minimal. Tout cela vise à
maintenir une surface ne pouvant pas emprisonner irréversiblement des
souillures ni être le siège d'une prolifération bactérienne non
éliminable par des conditions usuelles de nettoyage. La zone non
alimentaire doit être conçue pour empêcher la rétention d'humidité et
faciliter le nettoyage. Les critères de conception peuvent être moins
contraignants (rugosité, matériaux …).
Deux milieux agressifs
Les matériaux sont soumis à deux
principaux types de milieux agressifs:
le milieu alimentaire et le milieu de nettoyage.
Le milieu alimentaire peut être de toute
nature (lait vin, vinaigre,
moutarde, jus de fruit, saumure ... ). La tenue à la corrosion est
relativement bien maîtrisée dans la mesure où l'on connaît les
matériaux appropriés à chaque secteur alimentaire. Les données
bibliographiques (tables de corrosion ... ) donnent pour la plupart des
matériaux usuels des renseignements sur leur comportement dans les
milieux alimentaires. Des essais de laboratoires dans des milieux
simulateurs (acide lactique, acide citrique, chlorure de sodium) sont
susceptibles de renseigner sur le comportement à la corrosion des
matériaux non référencés. L'opération de nettoyage est en général
considérée comme faisant partie du procédé alimentaire. Dans certains
secteurs, les surfaces peuvent être soumises à des contrôles
biologiques de propreté de surface. Qu'il s'agisse de circuits ouverts
(nettoyage manuel avec ou sans pression) ou de circuits fermés
(nettoyage en place en circulation), le cycle de nettoyage fait appel à
des produits chimiques potentiellement agressifs pour les matériaux.
Les produits utilisés diffèrent selon les souillures à éliminer, leur
quantité et leur état de transformation (cuites, séchées ... ). Des
séquestrants, tels que l'EDTA (éthylènediaminetétra-acétique) ou
l'acide citrique, qui présentent un caractère complexant sont
généralement ajoutés dans les solutions de nettoyage pour éviter la
redéposition des souillures. Des inhibiteurs de corrosion peuvent
également être introduits notamment pour le nettoyage de certains
métaux, comme l'aluminium, sensible à la présence d'un milieu alcalin
ou comme l'acier inoxydable en présence de chlorures
La géométrie de la pièce est conçue en
fonction des impératives
appliques pour la tenue mécanique de l’ensemble lui-même et doit
minimiser les risques de corrosion. Une mauvaise conception peut
provoquer une corrosion prématurée d’un matériau théoriquement
résistant dans un milieu donné. Les situations à éviter absolument ont
donné en figures 3.11-3.35.
L’USURE DES ACIERS INOXYDABLES
De plus en plus se développe l'emploi
des aciers inoxydables pour la
réalisation de pièces mécaniques frottantes; c'est en particulier le
cas dans les domaines alimentaire, nucléaire, spatial; ces aciers sont
aussi couramment utilisés dans les mécanismes devant fonctionner dans
l'eau et plus encore dans l'eau de mer; de même, s'amplifie
l'utilisation des réfractaires austénitiques dans les applications à
hautes températures, etc.
En ce qui concerne le frottement, ces
aciers nécessitent, en raison de
leur très grande aptitude au grippage, des précautions d'emploi très
particulières.
Les principaux incidents que l'on peut
rencontrer sur des pièces
frottantes en acier inoxydable, sont:
1. LE GRIPPAGE.
On voit sur la figure 3.36 ce qui peut
se passer lorsqu'on fait frotter
deux pièces en acier inoxydable (dans le cas présent, il s'agit d'un
acier inoxydable austénitique ayant frotté sur un inoxydable
martensitique): il y a eu grippage. Dans ce cas, il s'agit d'un
grippage par soudure. Interprétation: sous l'effet combiné des hautes
températures engendrées micro-localement par le frottement et de la
déformation plastique des aspérités, les surfaces des corps frottants
sont placées dans des conditions telles que tous les phénomènes prévus
en théorie par la thermodynamique, la physique ou la chimie ont des
chances d'apparaître (diffusion, formation d'alliages, fusion suivie de
trempe, etc.); il en résulte entre les surfaces des corps frottants la
formation d'un nouveau matériau d'interface fabriqué à partir des
métaux et des ambiances en présence; si ce matériau a des
caractéristiques mécaniques supérieures à celles de l'un et de l'autre
des deux métaux en présence, le mouvement, pour se poursuivre, doit
déchirer le plus faible de ces deux métaux ; il y a donc transport sur
une des deux pièces du métal de l'autre (dans le cas de la figure 3.36
transport de l'acier inoxydable austénitique sur l'inoxydable
martensitique).
Il est d'autres cas où l'explication du
phénomène est un peu moins
aisée. Par exemple, on utilise très souvent le cupro-aluminium comme
antagoniste de l'acier inoxydable. Dans nombre de cas et en particulier
ceux où la lubrification est aléatoire, un tel couple de frottement
peut conduire au grippage. On peut donner au phénomène l'explication
suivante: pendant les premiers moments du frottement, le
cupro-aluminium subit des transformations physico-chimiques
superficielles qui se caractérisent visuellement par l'apparition d'une
coloration rouge à sa surface, l'analyse de ce composé de couleur rouge
révèle qu'il s'agit de cuivre pratiquement pur, or, le cuivre grippe
quasi instantanément sur l'acier inoxydable avec transport de cuivre
sur l'acier inoxydable. Autrement dit, c'est parce qu'en cours de
frottement, le cupro-aluminium se recouvre de cuivre qu'il devient apte
à gripper sur l'acier inoxydable.
Bien entendu, les phénomènes précédents
peuvent être considérablement
perturbés par l'ambiance dans laquelle baignent les mécanismes, en
particulier par les transformations physico-chimiques des matériaux
telles les oxydations.
En définitive, une des premières
conditions à respecter pour faire
frotter un métal X sur l'acier inoxydable est de choisir ce métal de
façon telle qu'il soit insoluble à la fois dans l'acier inoxydable et
dans les oxydes dont ce dernier peut se recouvrir. En pratique, le
choix de tels couples est difficile à faire a priori.
2. LES DECHIRURES SUPERFICIELLES PAR
SURTENSION.
On peut démontrer que lorsqu'un curseur
frotte sur une piste, celle-ci
est le siège à l'arrière du curseur de contraintes de tension dont la
valeur peut atteindre 2 f ∙ pm, où f est le coefficient de frottement
et pm la pression maximale au centre de 'empreinte d'appui.
On conçoit donc que si le matériau
constituant la piste a une
résistance à la rupture inférieure à cette valeur 2 f . pm, il
s'ensuivra des déchirures de la peau de la piste.
L'acier inoxydable est très sensible à
ce phénomène, qui est illustré
par les figures 3.37 et 3.38 qui représentent, vues par en dessus, les
surfaces de deux pièces en acier austénitique dont l'une a été mise
dans des conditions de frottement telles que les contraintes de tension
2 f . pm soient supérieures à la résistance à la rupture de l'acier et
l'autre dans les conditions inverses.
L'observation en coupe de telles
fissures montre qu'elles n'intéressent
(fig. 3.39) qu'une très faible profondeur en dessous de la surface, de
l'ordre de quelques microns; par contre, elles peuvent être à l'origine
d'une émission de particules avec pour aboutissement le blocage du
mouvement, c'est-à-dire ce que l'on appelle communément le grippage.
3. LE FLUAGE.
Ce phénomène est particulièrement
fréquent dans les cas de frottement
sous hautes charges ; en particulier, l'acier inoxydable austénitique y
est très sensible (figure 3.40). Deux cas sont possibles :
- ou bien le phénomène de fluage ne se
stabilise pas et dans ce cas la
géométrie des pièces peut être totalement perturbée;
- ou bien le phénomène de fluage se
stabilise et dans ce cas
l'écrouissage superficiel qui en résulte peut être très bénéfique du
point de vue frottement ; par contre, il peut y avoir des risques du
point de vue de la résistance des pièces à la corrosion.
PRINCIPALES CONDITIONS A RESPECTER POUR
FAIRE FROTTER UN ACIER
INOXYDABLE
A partir des observations précédentes,
on
peut énoncer ainsi les
principales conditions à respecter pour qu'un acier inoxydable frotte
dans des conditions acceptables:
- il faut d'abord intercaler entre les
deux pièces frottantes un
inhibiteur de soudure. Dans le cas des aciers classiques, il existe
beaucoup de ces inhibiteurs (couches d'oxydes, films lubrifiants
adsorbés, sulfure de fer, etc.) ; par contre, dans le cas de l'acier
inoxydable, le problème est rendu plus complexe, car il ne faut pas
sensibiliser le matériau à la corrosion;
- il faut ensuite réaliser à la surface
de l'acier inoxydable une
couche qui soit à la fois dure, ductile et homogène: dure pour pouvoir
résister au labourage par les aspérités de la pièce antagoniste,
ductile pour pouvoir suivre sans se briser d'éventuelles déformations
du substrat, homogène pour limiter au maximum l'effet des contraintes
de traction à l'arrière du curseur.
Or, un traitement de surface remplit ces
conditions
|