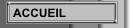
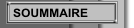
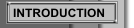
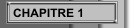
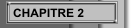
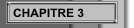
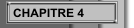
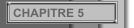
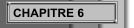
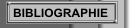
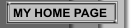
|
CHAPITRE 5
TECHNOLOGIES DE RENFORCEMENT SUPERFICIEL
Le développement des traitements et revêtements de surface est un
domaine prioritaire dans la mise en oeuvre des matériaux, avec pour,
objectifs l'amélioration de la résistance à la corrosion simple ou sous
contrainte, de la résistance à l'usure, de la résistance à la fatigue
ou encore de l'aspect esthétique La figure 5.1 rassemble les principaux
traitements superficiels applicables aux aciers inoxydables.
Les zones superficielles d'un composant sont directement exposées aux
agressions extérieures:
• à l'échelle microphysique, les défauts cristallins y sont en contact
avec l'environnement. Les dislocations s'y déplacent plus librement et
les domaines cristallins s'y déforment plus aisément qu'en pleine
matière ;
• à l'échelle macroscopique, les zones de concentration de contrainte
sont associées aux surfaces libres des pièces.
Les sollicitations statiques ou cycliques de flexion ou de torsion
génèrent des maxima de contrainte en surface.
Deux approches sont utilisées:
• modification d'une couche superficielle de la pièce par altération de
la microstructure initiale et/ou de la composition initiale;
• apport d'un revêtement extérieur sans altération ou avec une
altération mineure de la pièce originale.
Le tableau 5.1 rassemble les principaux traitements superficiels
applicables aux pièces qui travaille en industrie agro-alimentaire.
La résistance à l'usure est améliorée par l'augmentation de la dureté,
et la résistance à la fatigue et à la corrosion sous contrainte par la
génération de contraintes résiduelles de compression. Les deux effets
sont attribuables à la localisation dans une couche superficielle de la
formation d'une phase dure avec augmentation de volume, soit par
transformation martensitique, soit par précipitation.
TREMPE SUPERFICIELLE APRES CHAUFFAGE LOCAL
Ce type de trempe permet l’obtention d’une structure martensitique dans
une couche de quelques millimètres d’épaisseur. Le principe est le
suivant : Il consiste à amener rapidement le métal à sa température
d’austénitisation. Le refroidissement se fait au bout d’un temps très
court pour éviter le transfert thermique par conduction (autotrempe).
Aujourd’hui, nous connaissons 3 types de trempe après chauffage
superficiel :
• flamme (ou chalumeau)
• induction
• faisceaux de haute énergie (laser, électrons, plasma)
TREMPE SUPERFICIELLE PAR INDUCTION
Les premières recherches systématiques, concernant les effets
thermiques des courants induits remontent à 1887 [144]. En 1923, le
professeur RIBAUT de la Faculté des Sciences de Strasbourg, établissait
la théorie complète du chauffage par induction. Cependant, dès 1916
NORTHRUP, en Amérique procédait aux premiers essais pratiques. Une
première application à l'échelle industrielle, fût faite, aux USA en
1936, pour le traitement en chaîne d'arcanes de moteurs. En France, le
chauffage par induction en vue du traitement de pièces métalliques fût
utilisé pour la première foi à l'échelle industrielle en 1940, pour la
trempe en série de coiffes d'obus.
LE PRINCIPE
Dans la trempe par induction, l'induction ne sert en fait qu'à
échauffer la pièce sur une épaisseur donnée à la surface, jusqu'à une
température supérieure à Ac3 (pour les aciers hypoeutectoides) ou
supérieure à Acm (pour les aciers hypereutectoides). La zone chauffée
devient austénitique et la trempe provoque la transformation en
surface.
Principe du chauffage par induction
Le chauffage par induction d'une pièce d'acier est un phénomène
physique complexe. On peut dire que le chauffage par induction est une
application très directe à la fois de la loi d'induction - la loi de
LENZ - et de l'effet JOULE, par un dispositif approprié, qui est le
plus souvent un enroulement bobiné ou un solénoïde et qu'on appelle
"inducteur". (Figure 5.2).
On crée un champ magnétique alternatif, donc variable. Conformément à
la loi de LENZ, toute substance conductrice de l'électricité, si elle
se trouve dans ce champ magnétique variable, est le siège de forces
électromotrices d'induction appelées courants de Foucault, dissipant de
la chaleur par effet Joule, dans la substance même où elles ont pris
naissance [142].
Le chauffage par induction met en jeu trois phénomènes physiques
successifs:
1. transfert d'énergie de l'inducteur au corps à chauffer par voie
électromagnétique;
2. transformation en chaleur dans le corps de l'énergie électrique par
effet Joule;
3. transmission de la chaleur par conduction thermique dans la masse.
L'interaction entre le champ magnétique et le courant induit, entraîne
une distribution hétérogène du courant dans l'acier. Au centre de la
pièce, le courant est nul, par contre, il est maximal en périphérie.
La loi de décroissance est exponentielle
La bobine et le corps à chauffer peuvent être assimilables dans leur
principe à un transformateur. Les configurations d'inducteurs sont très
variées.
Principe du douchage
Le douchage (figure 5.3) consiste en un refroidissement de la pièce. On
peut appliquer différentes vitesses de refroidissement pour donner à
l'acier différentes caractéristiques.
Le douchage après un chauffage (figure 5.4) par induction est une
opération localisée qui permet d'obtenir une couche durcie d'épaisseur
limitée appelée couche superficielle ou profondeur de trempe ε. Le
refroidissement se fait après un temps relativement court pour éviter
que la chaleur ne diffuse vers le cœur du matériau, du fait de l'assez
bonne conductivité thermique des aciers traités. En général, les
trempes après chauffage par induction se font par un liquide de
refroidissement. Ce liquide peut être de l'eau, de l'huile ou un
liquide hydrosoluble dopé aux polymères.
Aspect théorique de la trempe par induction
Aspect théorique du chauffage par induction
Pour les applications industrielles, deux paramètres caractérisent
l'efficacité thermique et énergétique de l'induction. Il s'agit de l'
"effet de peau" qui caractérise la répartition des courants induits
dans la pièce (le champ magnétique alternatif qui pénètre dans le
matériau décroît rapidement pour disparaître et avec lui les courants
induits) et la puissance dissipée dans la pièce qui caractérise
l'efficacité du phénomène électrique. Enfin, de nombreux paramètres
interviennent : • la fréquence f du courant
• la nature du matériau
• le champ inducteur
• le couplage entre l'inducteur et la pièce à chauffer (entrefer,
longueurs respectives)
• le type d'inducteur et les caractéristiques géométriques
• la nature des conducteurs de l'inducteur
Epaisseur de zone de peau δ En combinant les équations de Maxwell et en
se plaçant dans l'approximation des courants de Foucault, on trouve une
expression de l'épaisseur de la zone de peau δ. δ: épaisseur de zone de
peau
ρ: résistivité du métal
μ0 :perméabilité du vide = 4∙10-7
μr :perméabilité magnétique relative pour un corps magnétique
f : fréquence utilisée
A la profondeur δ, appelée épaisseur de peau ou profondeur de
pénétration, l'amplitude du champ magnétique et donc celles du champ
électrique et de la densité de courant, valent 37% de l'amplitude en
surface. A une profondeur égale à 2 δ, l'amplitude de ces grandeurs a
décru de 87%. Ce phénomène est appelé effet de peau ou encore effet
Kelvin. Au-delà, les grandeurs électromagnétiques ont une valeur
négligeable.
La profondeur de pénétration dépend de la fréquence des courants. Plus
la fréquence est élevée, plus la profondeur de pénétration est faible.
D'autre part, cette profondeur de pénétration dépend également de la
nature du matériau, c'est à dire de sa résistivité électrique ρ et de
sa perméabilité magnétique μ. Or ρ et μ sont dépendants de la
température et c'est la principale cause du manque de corrélation entre
les épaisseurs de peau calculées théoriquement (par modélisation par
exemple) et les épaisseurs observées. La température empêche de
calculer précisément les profondeurs. A chaque instant, la température
change donc la puissance de chauffe et la profondeur de peau aussi.
Quand la résistivité du corps augmente, il en est de même de
l'épaisseur de peau δ.
Aspect théorique du refroidissement après chauffage superficiel
D'une manière générale, le refroidissement après chauffage superficiel
se fait par douchage ou par immersion.
De plus, on utilise différents liquides de refroidissement : • eau (à
différentes températures)
• huile
• eau + additifs
• air
Enfin, le temps de refroidissement de la pièce joue un rôle très
important puisque les transformations structurales du matériau
dépendent en partie de la vitesse de refroidissement (en °C/s).
En conséquence, on utilise ce manière approximative les diagrammes TTT
(Temps - Température - Transformation) ou TRC (Transformation en
Refroidissement Continu) pour donner à l'acier la structure voulue (et
donc la dureté), et TTA (Temps – Température - Asténitisation) adaptées
au chauffage superficiel.
Après trempe, la profondeur martensitique finale (appelons p=
profondeur de trempe) est inférieure à la pénétration de trempe .
C'est la trempabilité de l'acier qui a fait son effet.
CARACTERISTIQUES DE LA TREMPE PAR INDUCTION
La trempe par induction a des avantages ; et ceux-ci du point de vue
économique, métallurgique et mécanique.
Caractéristiques économiques
• Procédé à cycles rapides et non polluants.
• Son rendement énergétique global est excellent; chauffage limité en
temps et en volume aux seules quantités nécessaires.
• Les progrès accomplis dans les équipements permettent au fabricant de
répondre au besoin de l'utilisateur en ce qui concerne la définition
métallurgique du profil traité, et avec une grande régularité
indispensable pour la fabrication de grande série.
Caractéristiques métallurgiques
Il est important de savoir que les propriétés métallurgiques de la
microstructure ont une conséquence sur les propriétés mécaniques du
matériau.
Lors du chauffage de la pièce, lorsque l'on passe au dessus de Ac3, le
temps de maintien détermine le type d'austénite (homogène ou
hétérogène). Une austénite homogène donnera une martensite homogène. De
plus, la transformation α→γ dilate la microstructure et la trempe
contracte le réseau cristallin. Cet enchainement de transformation du
réseau génère des contraintes résiduelles qui sont à l'origine des
améliorations des propriétés mécaniques. En faisant des examens au
microscope optique, on remarquera la présence de martensite en surface.
Jusqu'à une certaine épaisseur, la microstructure relèvera ensuite des
plages de ferrites résiduelles et des plages de martensite. Enfin,
au-delà de la profondeur de trempe, la microstructure sera celle
qu’avait l'acier avant chauffage.
Remarque : La présence de ferrite n'est pas souhaitable car celle ci
peut être source de dislocations. A leur tour, les dislocations peuvent
générer des fissurations dans les plages de ferrites et ensuite dans
tout l'acier.
Enfin, lors du refroidissement par trempe, il se peut qu'on génère la
présence de tapures dues par exemple à une douche mal adaptée (débit
mal réglé, température "froide" au démarrage d'une installation).
Caractéristiques mécaniques
Propriétés mécaniques résultantes :
DURETE
Le profil de la couche est lié au profil de dureté. Celui ci se
décompose en 3 parties :
• une zone de grande dureté de structure martensitique qui correspond à
la profondeur de peau.
• une zone de structure mixte ferrite + martensite qui marque la zone
de transition.
• une zone de plus basse dureté qui correspond à celle du cœur.
FATIGUE
Les pièces traitées par induction ont de très bonnes résistances à la
fatigue. Cette tenue est associée aux contraintes internes (appelées
aussi contraintes résiduelles). Lors du chauffage, la couche externe se
dilate et le diamètre de la région chauffée est plus grand que le
diamètre initial. La pièce est ensuite trempée (figure 5.5):
• La peau se refroidissant la première, elle tend à se contracter mais
cette contraction est gênée par les couches sous-jacentes. Tant que les
couches superficielles sont austénitiques, elles vont seulement se
déformer plastiquement en s'écrouissant.
• Lorsque la transformation martensitique de la peau se produit,
l'accroissement spécifique du volume empêché par le cœur fait naître en
surface des contraintes résiduelles de compression.
• Enfin, il existe une zone chauffée mais non transformée entre la
surface et le cœur froid. Cet "anneau" de matière se refroidit à son
tour, mais sa contraction gênée par le cœur engendre des contraintes de
tension qui accroissent autant celles de compression.
Nous avons regroupé dans un tableau 5.2 les caractéristiques mécaniques
d'un acier traité par chauffage superficiel puis trempé.
INCONVENIENTS
La trempe par induction a certaines limitations, notamment liées à la
géométrie des pièces à traiter, à la précision des profils de trempe
obtenus, aux techniques de douchage et plus généralement au rendement
et à la reproductibilité des inducteurs.
Autre inconvénient important [145]: la mise au point peut être une
opération longue et coûteuse, si l'on n'a pas la chance d'avoir un
inducteur qui donne de bons résultats dès le démarrage.
Les agents de refroidissement les plus couramment utilisés après
chauffage inductif sont:
• l'air calmé ou soufflé;
• l'eau pure,
• l'eau additionnée d'accélérateurs régulateurs;
• l'eau additionnée de ralentisseurs régulateurs;
• les huiles de trempe et les polymères [148, 150].
• malgré ses inconvénients de pollution, le procédé de trempe à l'huile
par arrosage est quelquefois utilisé.
• les inconvénients de la trempe à l'huile sont les difficultés de
nettoyage bien que l'emploi des huiles lavables simplifie cette
opération, la pollution, la difficulté de passer sur un même bac de
l'huile à l'eau et la limitation sauf exception à la trempe par
immersion. Ces inconvénients ont conduit la fabrication de liquide
ininflammables qui, additionnée à l'eau lui confèrent les avantages de
l'huile (les solutions aqueuses de polymères).
La figure 5.6 présente la répartition des traitements thermiques par
types de traitement.
D'AUTRES ASPECTS
Depuis le début des années 50, le marché des équipements de trempe
superficielle par induction est en progression constante d'une
quarantaine d'installations / an correspondant à 10 à 15 MVA réseau.
Cette progression régulière est relativement peu influencée par la
conjoncture économique; ce phénomène s'explique d'après [32] par la
double amélioration de productivité et de compétitivité directement
associée à l'utilisation de cette technique.
La trempe superficielle par induction face aux technologies nouvelles
concurrentes. Les technologies concurrentielles dans le domaine des
traitements superficiels sont: le laser, le bombardement électronique;
les traitements thermochimiques (cémentation, nitruration,
carbonitruration etc..).
Tant que les deux premières n'auront pas fait de bonds significatifs,
quant à leurs performances et coûts d'accès, elles ne pourront
prétendre qu'à des applications spéciales. L'induction, quant à elle,
trouve ses limites dans le domaine des petites surfaces (petits
alésages, pignonnerie de tout petit module etc...)
Les traitements thermochimiques ne sont pas directement concurrentiels
de la trempe superficielle par induction, mais complémentaires. Ils
permettent en effet, d'atteindre des performances supérieures dans le
cas de la trempe "contournée" de pièces très chargées, avec des congés
de raccordement complexes, dissymétriques.
Toutefois, l'emploi de ces techniques a été fortement concurrencé par
la trempe par induction qui offre un bilan économique global plus
favorable et une bonne insertion dans un procès "tout en ligne" [32].
TRAITEMENTS SUPERFICIELS PAR LASER ET PAR FAISCEAU D'ELECTRONS
Les nouvelles sources à haute densité d'énergie, le tels que le laser
ou le faisceau e d'électrons, présentent un intérêt grandissant dans le
domaine des technologies non polluantes de renforcement superficiels.
Le laser et le faisceau d'électrons se situent pratiquement dans le
même domaine de densité d'énergie. Le laser présente plusieurs
avantages, comme la possibilité de travailler dans l'air ou d'être
transporté sur une grande distance, avec une absence de déviation
magnétique, mais il présente l'inconvénient actuel d'être limité au
niveau de la puissance, ce qui réduit les surfaces susceptibles d'être
traitées en un seul passage. Le faisceau d'électrons présente
l'avantage de ne pas avoir la même limitation en puissance que le
laser, mais il ne peut pas être transporté sur de grande distances et
nécessite à l'heure actuelle de travailler dans des enceintes sous
pression réduite.
Par rapport aux techniques classiques de durcissement sélectif, la
caractéristique importante de ces procédés est un flux d'énergie
interne qui entraîne des vitesses de chauffage extrêmement rapide. De
ce fait, quand un faisceau la heurte la surface d'un métal ferreux
atteint des température d'austénitisation après un temps d'interaction
très court (une fraction de seconde) tandis que le cœur du métal n'est
pas affecté, c'est-à-dire que le gradient de température à partir de la
surface est raide. En conséquence, quand la source de chaleur est
supprimée, il n'y a pas besoin de fluide de trempe externe, pour
produire la transformation martensitique dans la couche superficielle,
le cœur du matériau fourni un récepteur de chaleur approprié pour une
auto trempe [152].
Le principe de l'auto-trempe est la base de l'un des principaux
avantages, revendiqué a ces traitements (réduction de la pollution,
distorsion minimale etc...). D'autres avantages dérivent de leurs
bonnes possibilités de régulation (une sélectivité et une précision
plus grande de la zone traitée; une aptitude à traiter des surfaces
inaccessibles aux technologies classiques; la reproductibilité, la
souplesse) et de leur vitesse (grande vitesse de production).
Suivant le temps d'interaction entre le faisceau d'énergie, la matière
et les puissances mises en jeu, les traitements superficiels
envisageables peuvent être pour des densités de puissance croissantes,
le durcissement en phrase solide, la création d'alliages de surface et
la réalisation de phases micro cristallisés obtenus par glaçage de
surface, voire amorphes.
Figure 5.7 Diagramme de flux thermique - durée d'interaction entre le
faisceau d'énergie, la matière et la situation des différentes
possibilités de traitement superficiel [ 143].
PRINCIPE DU TRAITEMENT THERMIQUE AU LASER
Depuis l'invention du laser (Light Amplification by Stimulated Emission
of Radiation) dans les années 1950, son développement il conduit à des
unités industrielles robustes et fiables, employées dans de nombreux
procédés de travail des métaux, dont le perçage, la coupe et le
soudage. Son emploi comme outil de traitement thermique a été
sérieusement envisagé pour la première fois au début des anées 1970. Le
principe du traitement par choc laser est présenté dans la figure 5.8.
Fondamentalement, dans un laser, les atomes d'un gaz ou d'un cristal
(le milieu où a lieu le processus laser) sont excités à un état de
haute énergie par l'application d'une énergie électrique, ou lumineuse
(le stimulant). Une partie de cette énergie est relibérée sous forme
d'un faisceau de forte intensité, parallèle et cohérent de rayonnement
électromagnétique avant une longueur d'onde bien fixe, ou limitée à une
bande étroite, qui peut se propager sur de longues distances, sans
absorption, ni dispersion notable et peut être focalisé ou réfléchi par
des lentilles ou des miroirs classiques (figure 5.8). Différents lasers
opèrent a des longueurs d'ondes allant de l'ultraviolet à l'infrarouge.
LE PRINCIPE DU TRAITEMENT THERMIQUE PAR FAISCEAU D'ELECTRONS
La technologie du faisceau d'électrons est disponible depuis environ 35
ans et est maintenant largement adaptée comme un outil industriel
fiable pour le soudage ou d'autres applications. Le rendement global et
la précision élevés du faisceau lui ont permis d'effectuer des travaux
précédemment impossible. Néanmoins, à cause des frais d'investissements
élevés qu'il suppose, on ne s'est jusqu'à présent peu intéressé à ses
possibilités au point de vue traitement thermique. Maintenant avec
l'avènement des lasers pour durcissement de surface, l'intérêt de
l'application des faisceaux d'électrons dans le même domaine a repris
de l'importance. Le principe du traitement par faisceau d'électrons est
présenté en figure 5.9 et en figure 5.10 est présenté le traitement par
arc plasma.
La puissance dit faisceau d'électrons, sous forme d'un jet d'électrons
de forte énergie, est créée à l'intérieur d'un "canon" comprenant un
filament chauffé émetteur d'électrons, une anode qui accélère ces
électrons à travers un potentiel à haute tension, une bobine de
focalisation qui concentre le faisceau à une distance réglable de la
source et une bobine de déflexion qui sert à déplacer le faisceau comme
on le désire.
Contrairement aux lasers, la totalité du système, y compris la chambre
de travail, opère sous vide, toutefois, comme dans ce cas l'énergie
cinétique des électrons est transmise directement aux atomes de la
surface de la pièce (par exemple avec une tension d'accélération de 125
kV, les électrons pénètrent d'environ 0,04 mm dans l'acier) et comme il
ne s'agit pas d'absorption, un revêtement est inutile. Un vide "doux"
(typiquement 5•10-2 mm Hg,) est employé normalement dans la chambre de
travail;comme une chambre de traitement thermique classique à un volume
de 0,02 - 0,11 m3, la mise sous vide est rapide et des vitesses de
production élevées sont réalisables.
Le progrès qui a permis l'application pratique du principe précédent, a
été le développement d'un système de commande par ordinateur
programmable spécialisé, couplé avec un équipement de faisceau
d'électrons (figure 5.11).
|