
|
CAPITOLUL 3
|

|
Coroziunea otelurilor inoxidabile deformate
plastic
|
|
Pentru încercari
experimentale s-au folosit mai multe marci de
oteluri inoxidabile a carorcompozitie este prezentata în tabelul
3.1.
tinând seama de cele prezentate în capitolul 2 s-aucalculat
pe baza
formulelor publicate în literatura de specialitate principalele
puncte
critice, acaror valori sunt redate si în figurile 3.1÷3.3.
Tabelul 3.1.Compoziţia
chimică şi punctele critice ale oţelurilor inoxidabile utilizate pentru
încercări experimentale
|
Ol |
C |
Mn |
Si |
S |
P |
Cr |
Ni |
Cu |
Mo |
Ti |
Ms |
Md |
EDI |
E
Cr |
E
Ni |
I |
E´Cr |
E´Ni |
S |
1 |
0.07 |
1.38 |
0.37 |
0.013 |
0.015 |
17.9 |
9.5 |
0.17 |
0.33 |
0.001 |
-201.9 |
113.32 |
50.82 |
19.14 |
12.341 |
-0.77 |
19.4 |
12.46 |
31.89 |
2 |
0.1 |
1.15 |
0.52 |
0.012 |
0.014 |
17.5 |
11 |
0.18 |
0.18 |
0.6 |
-323.2 |
108.80 |
64.81 |
19.71 |
14.629 |
-5.77 |
18.9 |
14.76 |
33.64 |
3 |
0.03 |
1.42 |
0.34 |
0.018 |
0.045 |
17.2 |
15.8 |
0.11 |
2.78 |
0 |
-490.6 |
92.60 |
48.00 |
22.05 |
17.443 |
-14.75 |
23.6 |
17.52 |
41.12 |
4 |
0.48 |
0.4 |
0.48 |
0.011 |
0.029 |
19.51 |
0.26 |
0.08 |
0.22 |
0 |
-360.1 |
-83.58 |
198.74 |
20.8 |
14.884 |
2.42 |
20.9 |
14.94 |
35.87 |
5 |
0.13 |
1.45 |
0.38 |
0.014 |
0.035 |
18.1 |
7.62 |
0.52 |
0.25 |
0 |
-198.2 |
84.71 |
71.27 |
19.24 |
12.401 |
0.87 |
19.5 |
12.77 |
32.25 |
6 |
0.06 |
1.12 |
0.42 |
0.0008 |
0.035 |
18.2 |
9.2 |
0.15 |
0.3 |
0.31 |
-172.3 |
116.63 |
45.52 |
19.96 |
11.605 |
0.65 |
19.7 |
11.71 |
31.43 |
7 |
0.03 |
0.56 |
1.4 |
0.0005 |
0 |
19.6 |
9.9 |
0 |
0.3 |
0.21 |
-232.8 |
115.30 |
21.29 |
23.17 |
11.08 |
0.29 |
22.1 |
11.08 |
33.18 |
8 |
0.03 |
0.95 |
0.58 |
0.019 |
0.015 |
15.55 |
6.22 |
0.15 |
0.07 |
0.014 |
171.88 |
173.89 |
27.77 |
16.84 |
7.64 |
11.31 |
16.8 |
7.745 |
24.52 |
9 |
0.03 |
1.22 |
0.5 |
0.015 |
0 |
17.51 |
8.75 |
0 |
0.33 |
0.038 |
-71.44 |
138.79 |
31.78 |
19.06 |
10.26 |
3.57 |
19.2 |
10.26 |
29.43 |
|
Ms=1302-42%Cr-61%Ni-33%Mn-28%Si-1667(%C+%N)
[°C]
Md=413-462(%C+%N)-0,2%Si-8,1%Mn-13,7%Cr-0,5%Ni-18,5%Mo
[°C]
EDI=
25,7+2,0%Ni+410%C-0,9%Cr-77%N-13%Si-1,2%Mn
E
Ni=%Ni+%Co+0,5%Mn+30%C+0,3%Cu+25%N
E
Cr=%Cr+2%Si+1,5%Mo+5,5%Al+1,75%Nb+1,5%Ti+0,75%W
E´ Ni=%Ni+30(%C+%N)+0,5%Mn+%Cu
E´ Cr=%Cr+2%Mo+0,5%Si
S = E´ Cr + E´ Ni
I=37,19-51,2%C-1,02%Mn-2,59%Ni-0,467%Cr-34,4%N
|
|
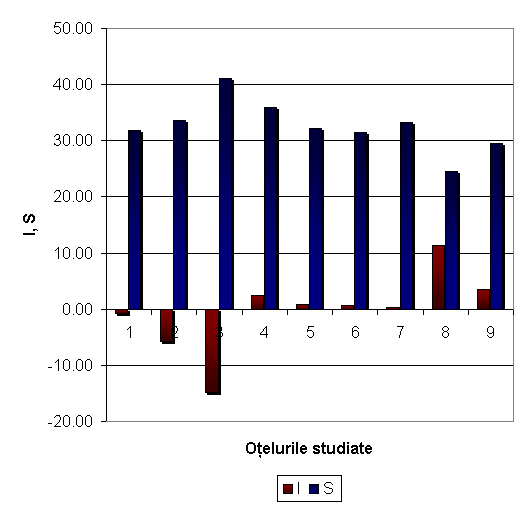
|
Figura 3.1. Coeficientii de
stabilitate si instabilitate pentru otelurile inoxidabile austenitice
|
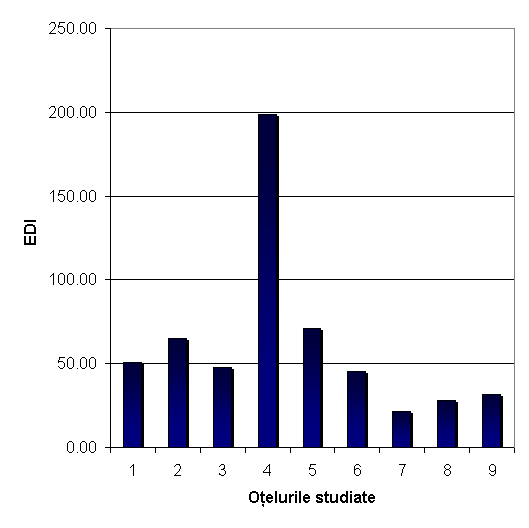
|
Figura 3.2. Energia defectelor de
impachetare, in mJ/m2 pentru diferite oteluri inoxidabile
austenitice
|
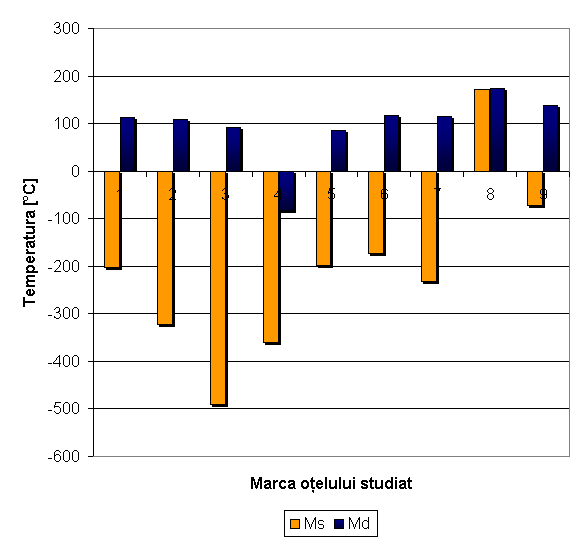
|
Figura 3.3. Punctele critice Ms si
Md pentru diferite oteluri inoxidabike austenitice
|
3.1.
Deformarea la cald si influenta ei asupra coroziunii
Studiul comportarii la deformare la cald a otelurilor
inoxidabile
autenitice s-a efectuat prinîncercarea de rasucire la cald.
Aceasta
metoda permite obtinerea unor grade de deformare relativmari fata de
celelalte metode si de asemenea viteze de deformare constante pe durata
încercarilor.Dupa ruperea probelor s-a determinat rezistenta la
coroziune a acestora. Deci încercarea a urmaritdoua aspecte,
în primul
rând obtinerea unor informatii legate de comportarea la deformare
si
apoimodul cum parametrii si conditiile de deformare influenteaza
rezistenta la coroziune.
Încercarile experimentale s-au facut pe otelurile
nr. 4
si 5 a caror
compozitii chimice, punctecritice si semnificative au fost prezentate
în tabelul 3.1.[237]
Epruvetele pentru rasucire la cald au fost prelevate
mecanic
din
bare laminate de ∅20mm,având forma si dimensiunile prezentate
în figura
3.1.1 [2576, 2545].

|
Figura 3.1.1. Dimensiunile
epruvetelor folosite la rasucire.
|
Încercarile s-au facut pe o instalatie de rasucire
la
cald existenta
la Catedra de DeformariPlastice din Universitatea Tehnica din
Cluj-Napoca [76], care prezinta urmatoarele particularitati:
▸poate masura momentul de torsiune si forta axiala ce
apare
în timpul deformarii;
▸se poate varia viteza de deformare, respectiv numarul
de
turatii pe minut, a axuluiprincipal.
Dispozitivul de încercare este prezentat schematic
în figura 3.1.2
si a fost realizat pornindu-se de la un strung care sa dea miscarea de
rotatie [76]. Axul 1, fixat în axul tubular 4, folosindu-se
lagarele
axiale 3 si piulitele 2, se poate roti în axul tubular 4 fara un
joc
axial. Axul tubular 4poate aluneca axial în suporturile 5 pe
lagarele
speciale 6. Pe axul 1 este fixat un suport 8 cusurubul 9 care tine
bratul 10. La celalalt capat al bratului este pus un lagar 11 care se
poatedeplasa usor de-a lungul suportului 12. Pentru echilibru sunt
fixate doua inele filetate 13 lacelalalt capat al suportului 8. Fiind
fixate timbrele tensometrice pe bratul 10, prin îndoireaacestuia
în
timpul deformarii, poate fi masurat momentul de torsiune. În
acelasi
fel este folositsuportu1 14, fixat pe axul tubular 4, care tine bratul
15 folosit pentru masurarea fortei axiale. Lacelalalt capat al bratului
15 este asezata piesa 16 care se aseaza fara miscare în piesa 17
si
carese poate roti în suportul 18. Suportul 18 poate aluneca
paralel cu
axul 1 între piesele 19, fixatepe placa 7. Pe aceiasi axa cu
piesele 18
sunt fixate pe placa de baza suporturile 20 în caresuruburile 21
pot fi
manipulate manual prin folosirea rotilor 22. Cu ajutorul suruburilor
21suportul 18 poate fi fixat într-o pozitie dorita prin folosirea
tuburilor 23, sau acesta poate fi presatîntr-o directie sau alta
cu o
forta dorita folosind arcul 23a în locul tubului 23.
Dispozitivulfunctioneaza pentru un moment de torsiune de 400 daN⋅cm si
o forta axiala de 300 daN. El estepus pe un strung, în locul
mesei
acestuia, putând fi fixat cu ajutorul suruburilor 24 si pieselor
25.Pe
axul principal al strungului a fost fixata piesa 26. Epruveta 27 se
monteaza pentru încercareîn axul 1 al dispozitivului si
piesa 26 de pe
axul strungului, prin intermediul pieselor schimbabile28, prin
însurubare.
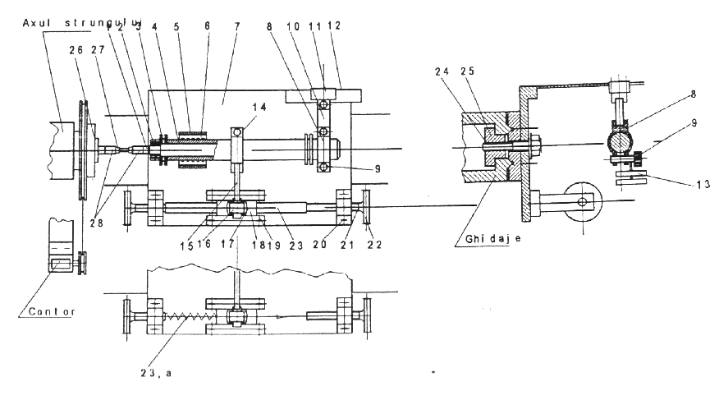
|
Figura 3.1.2. Schema dispozitivului
de încercare. |
În figura 3.1.3 se arataaspectul unei oscilograme
rezultatadin
rasucirea la 747°C a uneiepruvete din otel cu o viteza derasucire
de 22
rot/min. Aspectulcurbei de variatie a momentului derasucire este
similar cu celeprezentate în lucrarile [45, 218]pentru un otel
austenitic similar.Astfel în momentul atingeriivalorii maxime a
momentului areloc o modificare a sensului forteiaxiale, lucru care
poate fi pus în legatura cu procesul de recristalizare dinamica
care
are 1oc laaceste oteluri.
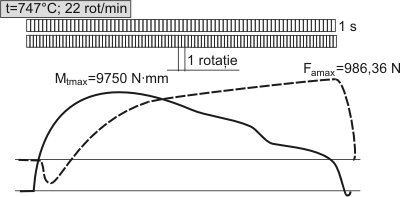
|
Figura 3.1.3. Oscilograma obtinuta
la rasucire.
|
Rezultatele experimentale obtinute sunt prezentate
în
tabelele 3.1.1÷3.1.4 si figurile 3.1.4÷3.1.7.
Rezistenta la deformare. În figurile 3.1.4
÷ 3.1.7 valorile rezistentei la deformare σ pentruun grad de
deformare ε=0,8 s-au calculat cu relatia:
Efortul tangential maxim τmax s-a
calculatdin
momentul maxim de rasucire Mmax,înregistrat
la începutul încercarii, cu relatia(3.1.1), unde m este un
coeficient
ce exprimasensibilitatea rezistentei la deformare fata deviteza de
deformare, având valorile 0,1 lat=900°C si m=0,2 la
t=1100°C si variind
liniarîn acest domeniu de temperaturi [256], R esteraza portiunii
deformate a epruvetei.
Deformabilitatea otelurilor
Apreciereadeformabilitatii
s-a
facut prin numarul de rasuciri pâna la rupere. În cursul
încecarilor de
rasucirela cald cu mentinerea fixa a lungimii epruvetelor au aparut si
eforturi axiale de tractiune cu valorimaxime pâna la 1,4 daN/mm2,
precum si eforturi de compresiune de 0,8daN/mm2.
Determinarea duritatii. Duritatea s-amasurat pe
probele
supuse încercarii dupa ceau fost sectionate longitudinal,
atât în
zonadeformata cât si în zona nedeformata.Masuratorile de
duritate s-au
facut înpunctele aratate în figura 3.1.8.
Rezultatelemasuratorilor de
duritate sunt prezentate înfigurile 3.1.9 si 3.1.10.
Din analiza rezultatelor legate de:rezistenta la
deformare,
deformabilitate siduritate se pot desprinde urmatoareleconcluzii:
1.Rezistenta la deformare scade cucresterea
temperaturii, asa
cumrezulta din figurile.3.1.4 si 3.1.6.Valorile rezistentelor la
deformare pentru cele doua oteluri studiate au valori
apropiate.Diferenta rezistentei la deformare dintre cele doua oteluri
se diminueaza în mare masuracu temperatura.2.Cresterea vitezei
dedeformare duce la marirearezistentei la deformare.
3.Continutul mai mare înelemente de
alieredetermina o
marire arezistentei la deformare.
4.Studiul variatiei duritatiipe adâncimea
probeievidentiaza faptul
cadatorita ecruisariisuperficiale duritatea estemai ridicata la
suprafata probei decât în interior.
5.În urma deformarii plastice la cald prin
rasucire se
observa ca duritatea la suprafata scadeîn jurul temperaturii de
900°C.
Testele de coroziune asupra otelurilor inoxidabile 35
MoCr165
si
12NiCr180 cu compozitiachimica din tabelul 3.1, deformate la cald cu
grade diferite de deformare prin rasucire, s-au facuttinând seama
de
rolul diferitilor factori care influenteaza mecanismul coroziunii fata
de mediileutilizate.
Metoda de experimentare la coroziune a fost prin imersia
totala a
probei în mediu, în conditiistatice, pentru a putea exprima
cât mai
bine starea termodinamica a otelului fata de agresivitateamediului si a
asigura o reproductibilitate buna.
Având în vedere ca, procesele de coroziune
în medii ionice
(umede,electrolitice) sunt denatura electrochimica, care se supun
legilor termodinamice electrochimice, s-au ales pentrustudiul
coroziunii metode ce se bazeaza pe testari electrochimice care permit
scurtarea durateide experimentare, marirea preciziei si stabilirea
aspectelor legate de cinetica coroziunii, mult maiapropiate de
realitate.
Influentele exercitate de diferiti factori (de mediu,
mecanici,
temperatura s.a.) asuprapotentialului electrochimic al otelurilor
inoxidabile se traduc direct prin stabilitatea sauinstabilitatea
termodinamica a otelului inoxidabil, privind coroziunea sa în
mediul
utilizat.
Tehnica de investigatie a fost voltametria ciclica, care
a
permis studiul interfetelorotel/oxid/mediu.
Masuratorile s-au facut într-o celula
electrochimica cu
trei
electrozi. Electrodul de studiat,E.S., format din otel inoxidabil
nedeformat, deformat sau la care s-au aplicat alte tratamente.
Potentialul electrochimic al electrodului de studiat s-a
masurat
fata de un electrod dereferinta. S-a folosit ca referinta electrodul de
calomel - KCl saturata (E.C.S.) A carui potentialeste constant si
cunoscut ( ε0 = +0,242 V). Electrodul de calomel are
extremitatea activa (capatul)sub forma unei capilare Haber-Luggin cu un
diametru minim, pentru a putea masura potentialulunor zone mici.
Capatul capilarei electrodului s-a asezat cât mai aproape de
suprafataelectrodului de studiat pentru a masura cât mai fidel
potentialul otelului si a elemina rezistentagrosimii stratului de
electrolit, a unor cauze ce produc efecte de ecranare sau modificare
arepartitiei densitatii de curent pe suprafata metalului. Pentru
polarizarea electrochimica aelectrodului de studiat s-a folosit un
electrod inert de platina, numit contra electrod (C.E.).
Mediul de coroziune a fost solutie 3% NaCl, deoarece
ionii de
Cl- constituie unul dintreagentii cei mai frecventi si mai
puternici de coroziune în solutie.
În timpul masuratorilor mediul de coroziune a fost
neagitat, pentru
a lasa ca transportul demasa sa aiba loc natural prin difuzie.
Celula electrochimica de coroziune a fost montata
în
instalatia prezentata schematic înfig.3.1.11
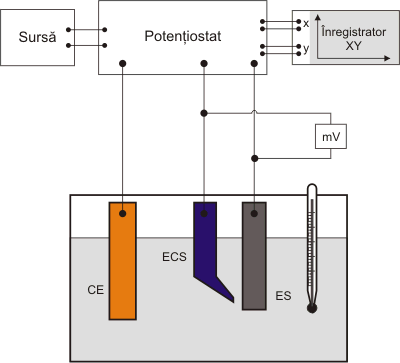
|
Figura 3.1.11. Schema instalatiei
experimentale pentru voltametrie ciclica.
ES electrod de studiat (piesa)
ECS electrod de calomel, KCl saturata
CE contraelectrod
|
Temperatura de lucru a fost 220±0,50.Cresterea
temperaturii în cazul masuratorilor în conditii statice ar
da nastere
la curenti deconvectie, care fac foarte dificila reproductibilitatea
rezultatelor.
La imersarea probelor supuse testului s-a tinut seama ca
adâncimea
de imersare a epruvetelorsub nivelul de suprafata a mediului sa fie
aceeasi la toate testele pentru a evita unele efecte deaerare
diferentiata a mediului deasupra probei.
Suprafetele epruvetelor pentru testare au fost curatate
si
degresate
cu alcool sau cu acetona.Pe fiecare proba s-a delimitat o suprafata de
circa 1cm2 care trebuia expusa testului de coroziune,iar
restul suprafetei a fost acoperita cu un strat de lac pentru a o izola
de actiunea mediului.
Sursa de curent continuu s-a ales mult mai puternica
decât f.e.m. a
celulei electrochimice(de coroziune), de exemplu 50 V sau chiar 100 V.
În acest mod s-a asigurat o constanta buna acurentului, fiiindca
reactiile si respectiv variatiile de tensiune cu care celula
electrochimica seopune sunt foarte mici comparativ cu sursa de
alimentare. Rezistenta variabila a fost aleasa devaloare mare (100ΩV )
pentru a putea asigura caderea necesara de tensiune.
Experimentarile au constat în înregistrarea
intensitatii curentului
care traverseaza interfatastudiata, ca urmare a modificarii din
exterior a potentialului electrochimic a sistemuluimetal/oxid/mediu
dupa o functie atribuita adecvat si cunoscuta, dE/dt.
Potentialul electrochimic al otelului de cercetat a fost
modificat între ES si CE de la ovaloare initiala fixa de -2V/ECS
(εi), spre valori pozitive ale tensiunii pâna la o
valoare finalade +2V/ECS (εf)- baleaj pozitiv (curba“dus”). εf
, este denumit si potential de inversare(întoarcere), când
modificarea
potentialului se face de aici în sens negativ pâna la
potentialulinitial-baleaj negativ (curba “întors”). Prin
conventie se
considera ca sensul pozitiv alpotentialului de electrod,
întâlnit în
literatura sub denumirea de “sensul nobil” este potentialulde coroziune
al metalelor nobile (Au, Pt etc.), care este mai pozitiv decât a
metalelor usorcorodabile, iar sensul negativ sau “sensul activ” este
asociat cu potentialul de coroziune almetalelor usor corodabile.
Curbele curent-tensiune au fost trasate cu o viteza de
baleiaj
de 20 mV/min pe unînregistrator XY pentru trei probe paralele.
Coroziunea otelului 35MoCr165 deformat la cald. În
figurile
3.1.12 - 3.1.14 suntprezentate curbele curent-tensiune, pentru otelul
inoxidabil 35MoCr165 nedeformat si deformatla 10500C cu 22
si 120 rotatii/min.
În timpul baleajului pozitiv în cazul
otelurilor
deformate la cald
cu cele doua turatii,fig.3.1.13 si 3.1.14 instalarea starii pasive
întârzie, potentialul începutului de pasivare
estedeplasat la valoarea
de +250 mV, cu 100 mV spre domeniul pozitiv, fata de potentialul
deînceput al starii pasive, la acelasi otel inoxidabil
nedeformat, la
care pasivarea începe de la 150mV, fig. 3.1.12.
La otelul inoxidabil nedeformat, starea pasiva,
când
valoarea
curentului de coroziune esteminima, se mentine pâna la 700 mV
(potentialul de pic). Peste aceasta valoare a potentialului,pelicula
pasivanta a otelului începe sa se distruga si se
înregistreaza o
crestere pronuntata acurentului de coroziune - respectiv a vitezei de
coroziune.
La proba deformata la 10500C cu 22 rot/min,
figura
3.1.13, starea pasiva se mentine pânala aproximativ 800 mV,
largimea
domeniului de pasivare fiind ca si la otelul nedeformat de 550mV, dupa
care se înregistreaza o crestere a curentului de coroziune cu o
panta
apropiata celei dela otelul nedeformat, pe când la otelul
deformat la
10500C cu 120 rot/min, fig 3.1.14 , stareapasiva se mentine
numai pânâ la aproximativ 1000 mV (stare cvasipasiva) dupa
care
curentul decoroziune creste evident.
Curentul de coroziune în zona de pasivare pentru
probele
nedeformata si cea deformata la10500C
cu 22 rot/min, este destul de scazut si cu valori foarte apropiate
între ele, cuprinse între0,05 μA pâna la 0,5-0,6 μA
în zona
potentialului de pic.
În cazul probei deformte la 10500C cu
120
rot/min,
curentul de coroziune în zona asa-zispasiva se mentine la valori
mai
ridicate cuprinse între 0,1 μA pâna la 1,35 μA în
zonapotentialului de
pic, cu tendinta de crestere aproape constanta spre domeniul
transpasiv. Deremarcat ca în cursul baleajului pozitiv, în
domeniul
transpasiv, valorile curentului de coroziune,pentru probele deformate
în cele doua conditii, sunt foarte apropiate între ele (de
la 1,5 μA
pânala 5,0 μA) si mult inferioare celor înregistrate pentru
proba
nedeformata, la care valorile suntcuprinse între 5,0 μA si 14,0
μA.
În cursul baleiajului negativ, reinstalarea starii
pasive se produce
cam la acelasi potential(≈1000 mV), atât pentru proba nedeformata
cât
si pentru cea deformata la 10500C cu 22 rot/min,figura
3.1.13 si 3.1.14 curba rosie, pe când la proba deformata la 10500C
cu 120 rot/min stareapasiva se reinstaleaza la aproximativ 650 mV. La
toate probele, stratul pasiv se mentine pe totdomeniul pasiv.
|
|
 |
Coroziunea
oteluilui
12NiCr180 deformat la
cald. Curbele
de
polarizare de baleiaj pozitiv(dus) curent-tensiune pentru otelul
inoxidabil 12NiCr180 nedeformat figura 3.1.15 aratainstalarea starii
pasive a otelului de la -150 mV, la un curent de coroziune scazut,
cuprins între0,025 μA si 0,3 μA pe un domeniu de potential de cc.
930
mV, pâna la potentialul de pic (de≈780 mV) când se trece
în domeniul
transpasiv. În zona de trecere pasiv/transpasiv
seînregistreza o
crestere neta a curentului anodic de dizolvare transpasiva a filmului
pasiv siconcomitent s-a observat o degajare puternica a oxigenului.
Pentru acelasi otel
12NiCr180, deformat cu aceeasi
turatie de
120
rot/min, starea pasiva seinstaleaza mai târziu comparativ cu cea
a
otelului inoxidabil nedeformat, potentialul începutuluipasivarii
este
deplasat spre valori pozitive în functie de temperatura la care
s-a
facut deformarea,figurile 3.1.16; 3.1.17 si 3.1.19. Astfel la otelul
deformat la 7500C, pasivarea începe laaproximativ
+350mV, se
mentine pe un domeniu doar de 200 mV, la un curent de pasivare destulde
ridicat, cuprins între 1,8 si 2,0 μA, pâna la potentialul
de +550 mV,
dupa care are loc trecereaîn domeniul transpasiv, unde se observa
pe
domenii înguste de potential tendinta de repasivare,mentinute
însa la
valori ridicate al curentilor de pasivare (în zonele 780-800 mV,
la
curentul depasivare de 2,7-3,0 μA; 1100-1200 mV, la curentul de
pasivare de 8,5-9,0 μA, mult mai ridicat).Trecerea de la domeniile
înguste de pasivare la cele active este marcata prin cresterea
evidentaa curentului de coroziune (la 950 mV si la 1200 mV). Pentru
otelul deformat la 900°C pasivareaîncepe la 220 mV, iar la
cel deformat
la 1050°C, la 280 mV.
Domeniul de mentinere a
stariipasive a otelului
12NiCr180
nedeformatsi deformat, la temperatura de 7500C,9000 C
si 10500C
cu viteza de rasucirede 120 rot/min, este reprezentat înfigura
3.1.20.
Din figura se poateevidentia, comparativ, intervalul depotential la
care pelicula pasivanta poatesa asigure otelului o rezistenta
lacoroziune. Se vede ca în urmadeformarii domeniul de rezistenta
lacoroziune , se îngusteaza de la otelulnedeformat , de 930 mV,
la 620
mV, lacel deformat la 10500C, la 590 mVpentru cel deformat
la 9000C (destul deapropiat de a celui de la 10500C)
si denumai 200 mV la cel deformat la 7500C.
Îngustarea foarte
pronuntata a domeniului de
pasivare,
deci reducerea zonei de stabilitate aotelului 12NiCr180 deformat la 7500C,
ar putea fi pus pe seama faptului ca la aceasta temperaturaare loc si o
sensibilizare la coroziune a otelului inoxidabil austenitic prin
precipitarea carburii decrom Cr23C la marginea grauntilor de
austenita.
Acest otel, la toate
conditiile de deformare
prezinta
în
zona pasiva
usoare tendinte dereactivare (ceea ce indica distrugerea partiala a
stratului pasiv) si de repasivare (refacereastratului pasiv), trecerea
de la starile de reactivare si repasivare se face relativ lent.
Curentul de coroziune,
(viteza de coroziune),
în
domeniul pasiv este
cel mai scazut la otelulnedeformat (în medie de 0,07 μA). La
otelul
deformat viteza de coroziune în domeniul pasiv(curentul de
coroziune)
este cea mai scazuta la cel deformat la 9000C (de 0,27 μA
în medie ),creste putin de la cel deformat la 10500C
(≈0,45 μA), iar la otelul deformat la 7500C curentul
decoroziune se mentine la valori destul de ridicate (≈1,9 μA).
La polarizarea în
sens negativ
(întors),
pentru
otelul nedeformat,
refacerea peliculeipasivante (starea pasiva) are loc la aproximativ
acelasi potential, cu un curent de coroziune totla fel de scazut ca la
polarizarea pozitiva, pe când la otelul deformat la 7500C,
curba polarizariinegative urmeaza alura asemanatoare celei de la
polarizarea pozitiva, însa la curenti de coroziunemult mai
scazuti, iar
la cel deformat la 9000C, repasivarea apare la un potential
mai pozitiv decâtla polarizarea pozitiva si se mentine la valori
foarte
scazute ale curentului de coroziune(aproximativ 0,06 mV).
De remarcat este faptul,
ca la otelul deformat la
10500C,
curentul în cursul baleajului negativ devine si ramâne
catodic, începând de la potentialul de ≈1100 mV.
La probele din otel
12NiCr180, deformatela 10500C,
însa
cu viteza de rasucire de 22rot/min figura 3.1.18, a rezultat o curba
de polarizare anodica (dus), ce nu prezinta un domeniu de pasivare
evident, curentul de coroziune creste progresiv în tot
cursulpolarizarii
pozitive. Cresterea este mai putinaccentuata între 250 mV si 450
mV,
dar multmai accentuata de la 450 mV pâna la 1500mV. Aceasta,
indica
faptul ca la deformareaotelului inoxidabil, s-a deteriorat în
mare
partestratul pasivant si nu are posibilitatea sa sereformeze pe tot
parcursul polarizarii pozitive.În cursul polarizarii negative,
curentul
devinesi ramâne catodic, începând de la potentialul
de ≈1100 mV, ca si
la otelul deformat la 10500Ccu 120 rot/min, figura3.1.19.
Aceasta s-ar putea datora descarcarii unor ioni care au provenit
dinreactia anodica de coroziune.
În figura 3.1.21
s-a prezentat curentul de
coroziune din
domeniul pasiv pentru otelul12NiCr180 nedeformat si deformat la 7500C,
9000C, 10500C.
Se vede ca la aceeasi viteza derotire de 120 rot/min, temperatura de
deformare influenteaza viteza de coroziune în domeniupasiv a
otelului
inoxidabil austenitic (înregistrata prin curent de coroziune
în domeniu
pasiv).
Din figura 3.1.21 se
observa ca la temperatura de
750°C
stratul
pasiv se mentine la un curentde 2µA, iar la 1050°C se observa
o
crestere a curentului în domeniul de pasivare pâna la
0,5µA.Aceste
variatii ale curentului de pasivare cu temperatura la aceeiasi turatie
se pot explica prinfaptul ca la 750°C are loc o sensibilizare la
coroziune a otelului inoxidabil [129]. Aceastasensibilizare este
datorata în principal intensificarii procesului de precipitare a
carburilor de cromla marginea grauntilor si ca urmare în zonele
învecinate marginii grauntilor concentratia de cromscade sub
limita de
inoxidabilitate.
La 900°C stratul
pasiv se reface, curentul de
coroziune
în domeniul
pasiv scade, aceastaexplicându-se prin faptul ca temperatura
fiind mai
ridicata viteza de difuzie a cromului este mai mare si ca urmare are
loc
o uniformizare a concentratiei de crom în otel.
Influenta vitezei de
rotatie în timpul
deformarii
la
aceeasi temperatura 10500C,
asuprapotentialelor stationare ale otelurilor 35MOCr165 si 12NiCr180,
stabilite înainte de aplicareapolarizarii, este prezentata
în figura
3.1.22.
Se vede ca potentialele
stationare ale celor doua
oteluri se
deplaseaza spre valori pozitivecu cresterea vitezei de rotire în
timpuldeformarii. Aceasta ar indica o oarecarecrestere a stabilitatii
otelului în mediude NaCl 3%, în conditii statice,
faraaplicarea
polarizarii.
Pe de alta parte, la
aceeasi vitezade rotatie,
temperatura de
deformare nuinfluenteaza semnificativ potentialulstationar asa cum
reiese dinreprezentarea din figura 3.1.23.
Din rezultatele si
discutiileprezentate mai sus,
se pot
desprindeurmatoarele concluzii:
- Structura obtinuta în urmadeformarii are
influenta
asupracoroziunii otelurilor, un rolimportant având însa
sicompozitia
chimica.
- Prin deformarea la cald, atât în
cazulotelului
35MoCr165 cât si a
otelului12NiCr180 domeniul de pasivare seinstaleaza
începând numai de
lapotentiale pozitive mai mari fata depotentialele de început de
pasivare aotelurilor nedeformate care pot aveachiar valori negative,
cum este cazulotelului 12NiCr180.
- Domeniul în care otelul 35MoCr165
sementine
în
stare pasiva (cu
rezistenta la coroziune) se îngusteaza cu marirea turatiei pentru
aceeasi
temperatura si este mai restrâns comparativ cu domeniul pasiv a
aceluiasi otel nedeformat.
- Viteza de coroziune a otelului 35MoCr165
deformat cu o
turatie
de120 rot/min este maimare decât viteza de coroziune la o
deformare cu
o turatie de 22rot/min, la aceeiasitemperatura (1050°C). Viteza de
coroziune la otelul nedeformat este mai mica decât aotelului
deformat.
- Pentru otelul 12NiCr180 deformat cu aceeasi
turatie,
temperatura
de deformareinfluenteaza comportarea la coroziune a otelului. Astfel
otelul deformat la 7500C, are ceamai scazuta rezistenta la
coroziune. Aceasta scadere a rezistentei la coroziune a
oteluluideformat la 7500C
poate fi pusa si pe seama faptului ca la aceasta temperatura
otelulaustenitic sufera o sensibilizare la coroziune prin precipitarea
carburii de crom Cr23C lamarginea grauntilor de austenita.
- Potentialele de început a domeniului de
pasivare
a
otelului
12NiCr180, au valori pozitivemai mari pentru toate conditiile de
deformare la clad fata de potentialul de început depasivare a
aceluiasi
otel nedeformat. Prin urmare deformarea otelului
îngusteazadomeniul
potentialului de pasivare.
3.2.
Deformarea la rece si influenta ei asupra coroziunii
Deformarea la rece a
otelurilor inoxidabile
austenitice s-a facut prin rulare si prin refulare.
a)
Deformarea prin rulare
În cadrul
încercarilor experimentale
s-a
folosit metoda de durificare prin rulare cu bila.
Dispozitivul utilizat, sprijinit pe doi rulmenti, este prezentat
în
figura 3.2.1. Acest dispozitiv s-a
montat pe dispozitivul port-cutit al unui strung paralel si
functioneaza în felul urmator: cu
mânerul 1 se roteste tija filetata 2, care comprima arcul
helicoidal 3,
prin aceasta asigurând forta
de apasare necesara. Forta se transmite prin cepul 5 al furcii 7, pe
care sunt montati rulmentii
cu bila 8, pe care se sprijina bila 9, care constituie elementul de
lucru al dispozitivului. Între
corpul 4 si furca 7, prin constructie se asigura un joc de 2-3 mm. La
contactul bilei cu suprafata
de durificat, asigurat prin deplasarea suportului port-cutit în
care
este montat dispozitivul de
durificare, se urmareste reducerea jocului dintre corp si bucsa la
jumatate, ceea ce asigura
apasarea bilei cu forta reglabila prin comprimarea corespunzatoare a
arcului helicoidal. Prin
rotirea piesei fixata în universalul strungului, bilei i se
imprima o
miscare de rotatie, care
combinata cu miscarea de avans asigurata de mecanismul strungului,
produce tasarea metalului
în zona de contact, ceea ce determina netezirea si durificarea
suprafetei. Arcul helicoidal 3
dezvolta o forta de apasare de 7,5 daN, la o rotatie a tijei filetate 2.
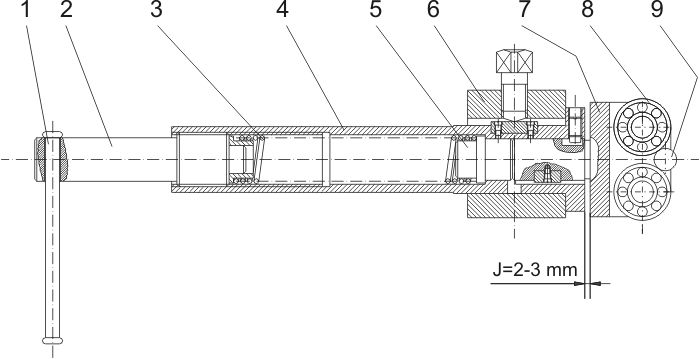
|
Figura
3.2.1. Schema dispozitivului de rulare
|
Aceste încercari
s-au facut pe otelul nr.6
cu
compozitia chimica: 0,06% C, 1,12% Mn,
0,42% Si, 0,008%S, 0,035% P, 18,2% Cr, 9,2% Ni, 0,15% Cu, 0,3% mo,
0,31% Ti, prezentata
în tabelul 3.1.
Fortele de apasare la
rulare, utilizate în
experimentari, sunt trecute în tabelul 3.2.1. Se
observa ca forta de apasare la rulare modifica rugozitatea Ra
si duritatea suprafetei. Astfel, cu
cresterea fortei de apasare la rulare creste duritatea. În ce
priveste
rugozitatea, în general scade
cu cresterea fortei de apasare la rulare.
Tabelul
3.2.1. Influenta fortei de apasare la rulare asupra rugozitatii
si duritatii. |
Nr.
probei
|
Forta
de
apasare daN
|
Rugozirarea
Ra, μm
|
Duritatea
HV5
|
1
|
70
|
0,17-0,18
|
360-362
|
2
|
80
|
0,16-0,15
|
390-392
|
3
|
85
|
0,15-0,14
|
435-437
|
4
|
0
(stare
initiala)
|
0,79-0,75
|
200-215
|
|
Comportarea la coroziune
a otelului nr. 6
(tabelul 3.1), deformat prin rulare, s-a facut prin
masuratori electrochimice de cronopotentiometrie, prin metoda
indicatorilor, cu solutie feroxil si prin examinarea optica directa.
Instalatia folosita la
determinarile
cronopotentiometrice este prezentata în figura 3.2.2.
Aceasta consta din: 1- celula electrochimica în care se produce
corodarea probei, 2- proba din
otel inoxidabil nedeformat si deformat prin rulare, 3- electrodul de
referinta. S-a folosit drept
electrod de referinta, electrodul de calomel saturat, care are
potentialul de 0,242 V la 25°C, cu
un coeficient de temperatura la 10°C de -0,007V. Acest electrod da
rezultate bune în mediu de
NaCl cu pH de 6-6,8, deoarece nu pot aparea potentiale de contact
lichid-lichid ca sa deranjeze
masuratorile. Capacitatea celulei de coroziune s-a stabilit
tinând
seama de reactivitatea mediului
fata de materialul supus coroziunii, marimea probei si durata
masuratorilor, în asa fel încât
concentratia produselor de coroziune în mediu sa fie mica. S-a
mentinut
în toate masuratorile
100 ml solutie coroziva la 1cm2 proba. Potentialul σ are rol
de a mentine constanta tensiunea
în cazul în care se aplica o tensiune exterioara
între proba de studiat
si alt electrod.
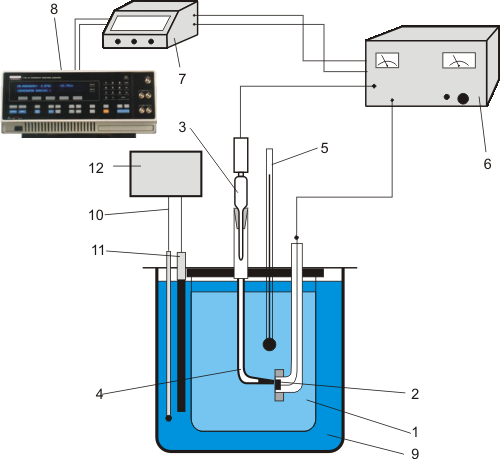
|
Figura 3.2.2. Schema instalatiei
pentru masuratori cronopotentiometrice la coroziunea libera:
1- celula electrochimica pentru coroziune;
2- proba de studiat;
3- electrod de referinta;
4- punte salina (soluþie KCl saturata);
5- termometru;
6- potentiostat;
7- milivoltmetru electronic;
8- culegerea si prelucrarea datelor;
9- baie de termostatare;
10- termometru;
11- încalzitor;
12- releu de temperatura.
|
Înainte de
introucere în mediu
coroziv,
probele au fost bine degresate cu solventi organici.
Pentru o repartizare cât mai uniforma a curentilor de coroziune
si
eliminarea efectului de
margine, s-a delimitat pe fiecare proba o suprafata de 1 cm2,
iar restul suprafetei a fost acoperita
cu un lac rezistent în mediul coroziv utilizat.
Ca si în cazul
deformarii la cald, s-a
folosit drept mediu coroziv o solutie de 3% NaCl.
Determinarile s-au facut la 25+1°C, cu suprafata deschisa a
mediului
fata de atmosfera.
Tensiunea electromotoare
a pilei de coroziune
s-a masurat cu un milivoltmetru electronic,
iar rezultatele au fost prelucrate si trasate diagramele εs(V)-timp(min),
pe calculator (figura
3.2.3.).
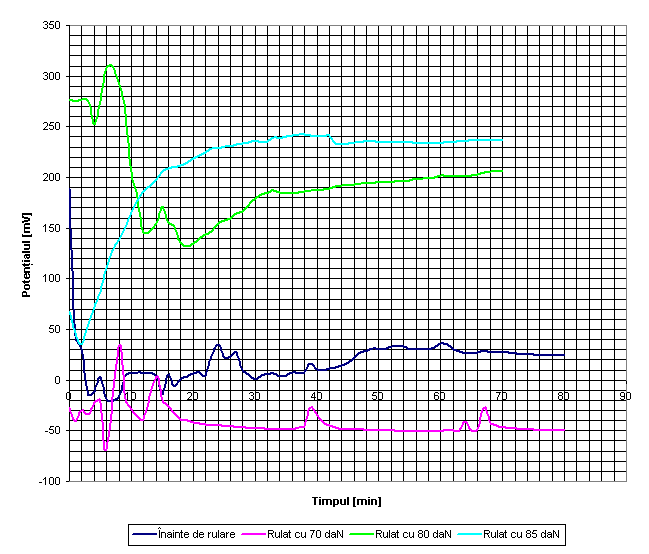
|
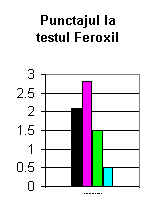
|
Figura 3.2.3. Diagrame
cronopotentiometrice a otelului inoxidabil austenitic 6 (v. Tab. 3.1),
în 3% NaCl la 25°C
|
Se vede ca, potentialul
de coroziune care
este o masura a fortelor electrochimice care
actioneaza la interfata metal/ mediu coroziv, variaza diferit în
raport
cu forta de apasare la
rulare. Cum fortele electrochimice de la interfata otel (conductor
electronic) si mediu
(conductor ionic) impune un transfer de electroni cu directie si sens
bine definite la suprafata
lor de separatie si nu în masa metalului sau a mediului, se poate
deduce ca la deformarea prin
rulare se produc modificari în straturile superficiale ale
otelului,
care se traduc prin modificarile
de potential electrochimic al acestuia.
Astfel, otelul
nedeformat în primul moment
are un potential de 189mV, dar în timp scade,
devenind electronegativ, ajungând chiar la valori negative de
pâna la
-21mV dupa 8 minute.
Deplasarea potentialului
spre valori negative
arata o crestere a instabilitatii aliajului în
mediul utilizat, si prin aceasta, o mai mare posibilitate de coroziune
datorita extinderii
portiunilor unde pelicula protectoare a fost distrusa si o suprafata
tot mai mare a metalului a
ramas descoperita si expusa coroziunii.
Dimpotriva, deplasarile
intermitente ale
potentialului spre valori electropozitive, arata
acoperirea partiala a suprafetei probei cu produse de coroziune,
însa
valoarea potentialului
ramâne la valori pozitive, dar scazute.
Otelul deformat cu cea
mai mica forta de
rulare are potentiale electrochimice apropiate
fata de otelul nedeformat pe aproape toata durata încercarii,
exceptând
minutele 7 si 13, unde
se observa o pozitivare însemnata a potentialului electrochimic
al
otelului, ceea ce arata o
refacere pe timp foarte scurt a peliculei de pasivare, dupa care
aceasta este distrusa si coroziunea
devine în continuare mai evidenta decât a otelului
nedeformat.
Intensificarea coroziunii în acest
caz poate fi pusa pe seama faptului ca la aceasta forta de apasare,
în
suprafata metalului se
înmagazineaza energii suplimentare, imprimând în
anumite zone stari
metastabile ale metalului,
care duc la aparitia unor tensiuni în suprafata.
Potentialul
electrochimic al otelului rulat
la forta de apasare de 80 daN porneste de la valori
semnificativ pozitive (cu buna stabilitate la coroziune), se deplaseaza
spre valori negative,
ramânând însa în domeniul de potential pozitiv,
apoi creste si prezinta
o tendinta de pasivare la
un potential de 195-200 mV. Otelul deformat prin rulare la 85 daN are
în faza de început un
potential pozitiv, dar mai scazut decât otelul rulat la forta de
apasare de 80 daN, însa se
deplaseaza continuu spre potentiale electropozitive (îsi mareste
stabilitatea la coroziune),
atingând dupa numai 14 minute o stare stationara de pasivare
stabila la
potentialul de 236 mV,
cel mai electropozitiv comparativ cu celelalte grade de rulare.
Cresterea stabilitatii
la coroziune cu
marirea fortei de rulare pentru probele rulate cu 80 si
85 daN poate fi explicata prin faptul ca odata cu cresterea fortei de
apasare la rulare, scade
rugozitatea si implicit se reduce suprafata reala a metalului supusa
coroziunii, figura 3.2.4.
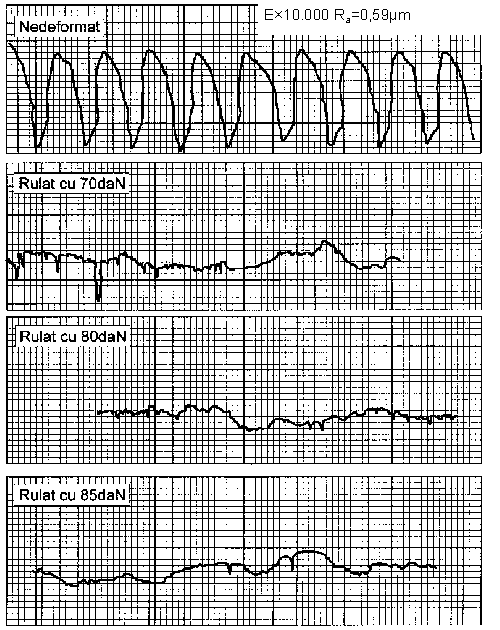
|
Figura 3.2.4. Profilul pisei din
oþel inoxidabil austenitic rulat cu diferite forþe de
apãsare (×10.000).
|
Paralel, pe probele
rulate s-au facut si
teste folosind metoda indicatorilor, care se bazeaza
pe culoarea caracteristica pe care o dau în prezenta unui
indicator,
mediul coroziv cu ionii
metalului ce trec în mediu în urma procesului de coroziune.
Pentru otelurile
inoxidabile, în care
elementul majoritar este fierul si în acelasi timp
principalul element din oteluri care trimite ioni în solutie (se
corodeaza), se foloseste solutia
feroxil cu urmatoarea compozitie: 1g/l K3[Fe(CN)6]
2H2O; 10g/l NaCl, 10g/l agar-agar, în apa
deionizata.Se adauga agar-agar pentru a se obtine o solutie de
consistenta gelatinei, care
împiedica întinderea rapida a zonelor colorate. Testul este
semnificativ îndeosebi în cazul
coroziunii pronuntat localizata (coroziune în puncte, fisuranta
etc)
cum este cazul otelurilor
inoxidabile. Se pot pune în evidenta porii existenti în
peliculele
protectoare de oxizi, nitruri
etc.În porii stratului protector de oxizi, nitruri s.a., otelul
nefiind
protejat, este supus coroziunii,
si din aceste portiuni, fierul din otel trece în mediu sub forma
de
ioni Fe2+. Aceste zone devin
anozi. Ionii de Fe2+ rezultati din coroziune, reactioneaza
cu fericianura de potasiu si formeaza
fericianura feroasa, de culoare albastru intens:
2K3[Fe(CN)6]
+ 3FeCl2
→ Fe3[Fe(CN)6]2 + 6KCl
Pe portiunile care se
corodeaza (anodice)
apare o culoare albastra, permitând astfel sa se
determine si pozitia zonelor anodice care se corodeaza si se coloreaza
în albastru si a punctelor
catodice care nu se corodeaza si ramân incolore.
Pentru a avea o
apreciere a coroziunii
privind metoda indicatorilor, s-a întocmit o scara de
valori dupa numarul de puncte pe cm2, prezentat în
tabelul
3.2.2.
Tabelul
3.2.2. Scara de valori
dupa numarul de puncte de coroziune în testul cu solutie
feroxil |
Punctajul
la
testul
feroxil
|
Aprecierea
atacului
coroziv
|
0
|
Fara
atac -
stabilitate
mare
|
1
|
Atac
slab -
puncte
slabe
albastre fara aglomerari - stabilitate relativa
|
2
|
Atac
moderat
-
puncte
albastre
cu mici aglomerari - stabilitate relativa
|
3
|
Atac
puternic
-
pete
albastre
cu aglomerari de produsi de coroziune pe
probe - instabilitate pronuntata
|
|
Testul feroxil pentru
otelul deformat prin
rulare este prezentat în figura 3.2.3b. Se constata
o buna concordanta între acest test si masuratorile
cronopotentiometrice care arata ca potentialul
electrochimic al otelului deformat este cu atât mai negativ, cu
cât pe
suprafata avem mai multe
puncte de coroziune.
b)
Deformarea prin refulare
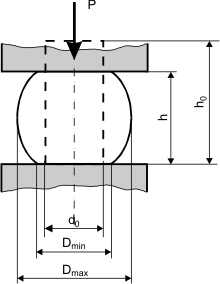
|
Figura
3.2.5. Schema refularii
|
În urma refularii
are loc o micsorare a
înaltimii
initiale a probei, crescându-i sectiunea transversala (figura
3.2.5). Gradul de deformare realizat prin refulare se poate
exprima, dupa STAS 2233-80, prin gradul de refulare
relativ X si prin refularea specifica n folosind formulele
urmatoare:
|

|
|
unde:
h0
este înaltimea initiala a probei, înainte
de refulare , în mm;
h-înaltimea finala a epruvetei, dupa
refulare, în mm.
|
Tensiunea principala
maxima σ1
este asigurata de
forta de deformare P, care determina deformatia maxima σ1
în
sensul micsorarii înaltimii
semifabricatului iar tensiunile σ2 si σ3 apar
în
plan transversal datorita fortelor de frecare.
Delimitarea zonelor de
deformare într-o
proba
refulata este prezentata în figura 3.2.6.
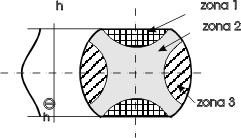
|
Figura
3.2.6. Delimitarea zonelor de deformare într-o epruveta
refulata
[76].
|
În zona 1
deformatiile sunt minime,
deformatiile
maxime se afla în zona 2 si deformatiile medii sunt în
zona 3. Deformatiile vor fi neuniforme si în intervalul
aceleiasi zone.
Probele din otelurile
7,8 si 9 (∅8x15;
∅10x15) au
fost refulate pe prese hidraulice de 20tf si 30tf, la grade
de deformare cuprinse între 20 si 60%.
Masuratorile
cronopotentiometrice sau
expunere
la coroziune libera pe otelurile 2, 3, 7, 8 si 9 (tabelul
3.1) deformate prin refulare cu diferite grade de deformare au pus
în
evidenta modificari ale
potentialelor electrochimice ale otelurilor ca urmare a deformarii.
Pentru otelul inoxidabil 2
(tab. 3.1), stabilizat cu titan si cu un procent apreciabil de nichel,
potentialele electrochimice ale
otelului la grade mici de deformare 20% si 30%, au valori apropiate,
dar negative, fata de
potentialul probei nedeformate, curbele potentiometrice
intersectându-se între ele dupa anumite
intervale de timp, figura 3.2.7a.
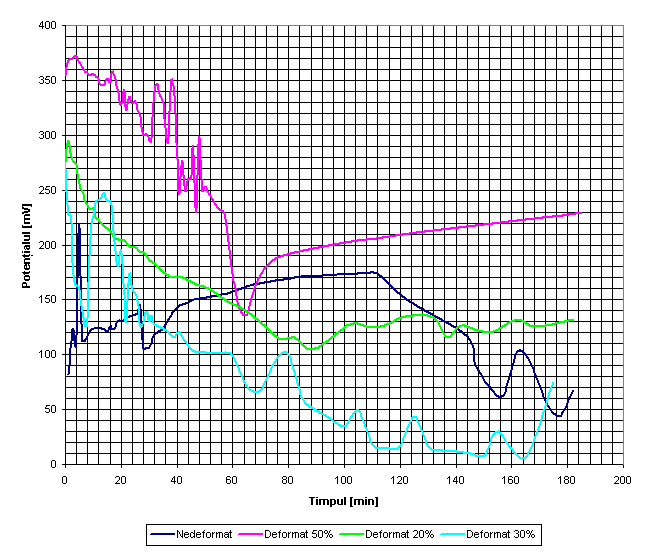
|
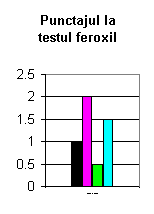
|
Figura 3.2.7. Diagrame
cronopotentiometrice în 3% NaCl la 25°C (a) si
punctajul la testul feroxil (b) pentru otelul inoxidabil austenitic 2
(tab. 3.1) deformat prin refulare.
|
Aceasta indica faptul ca
pentru otelul
inoxidabil 2, deformarea prin refulare la grade relativ
mici de deformare nu modifica esential probabilitatea termodinamica
privind comportarea la
coroziune a otelului. La un grad mai mare de deformare, de 50%,
variatiile rapide de potential
în sens pozitiv si negativ arata însa un proces continuu de
distrugere
si refacere a peliculei
protectoare care dupa cca. 50 minute prezinta o deteriorare pronuntata
si o scadere brusca a
potentialului deci scaderea rezistentei la coroziune. Testul cu solutie
feroxil pentru otelul 2
(tabelul 3.1) prezentat în figura 3.2.7b, arata o corespondenta
între
variatia potentialelor
electrochimice si porozitatea stratului protector.
La otelul 3 (tabelul
3.1) aliat si cu Mo si
cu un continut de 15% Ni, masuratorile
cronopotentiometrice prezentate în figura 3.2.8a, arata o
deplasare a
potentialului electrochimic
al otelului spre valori negative, cu instabilitate termodinamica mai
pronuntata, cu cât gradul de
deformare este mai mare. Se vede ca în zona de deformare 3
(figura
3.2.6), cu gradul de
deformare mediu, potentialul electrochimic are valori pronuntat
negative si cu tendinta
pronuntata la coroziune. Potentialul electrochimic în zona de
deformare
1 (figura 3.2.6), unde
deformarea este minima arata o tendinta mai pronuntata spre coroziune
decât starea
nedeformata, dar mai stabil decât zona cu deformarea medie.
Testul cu
solutie feroxil arata
aceasi tendita mai pronuntata la coroziune cu cât gradul de
deformare
este mai mare, figura
3.2.8b.
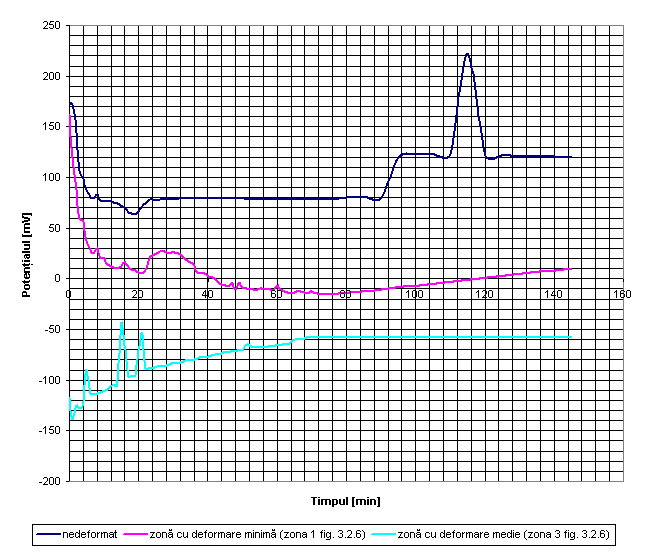
|
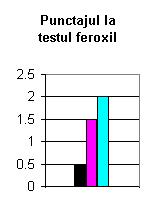
|
Figura 3.2.8. Diagrame
cronopotentiometrice în 3% NaCl la 25°C (a) si
punctajul la testul feroxil (b) pentru otelul inoxidabil austenitic 3
(tab. 3.1) deformat prin refulare.
|
Otelul inoxidabil 7
(tabelul 3.1), cu un
continut de 9,9% Ni, practic nealiat, si cu Ti si Mo,
în urma deformarii îsi modifica potentialul electrochimic
spre valori
negative, deci cu tendinta
mai pronuntata spre a se coroda, comparativ cu starea nedeformata,
însa
valorile potentialului
ramân în domeniul pozitiv, figura 3.2.9a.
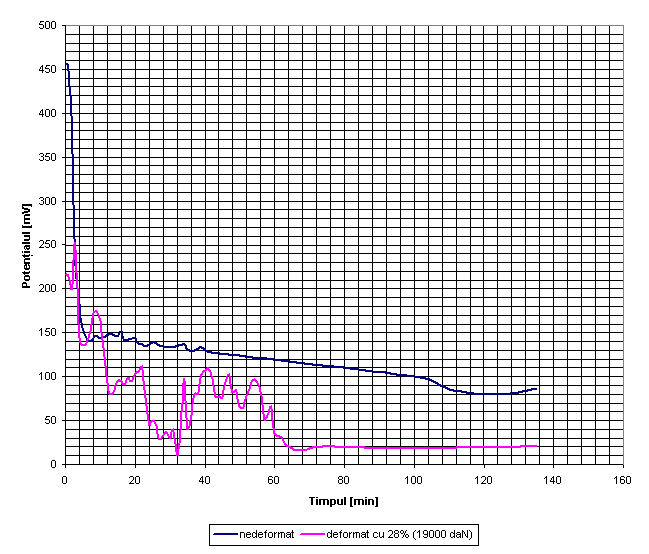
|
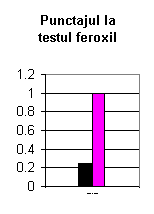
|
Figura 3.2.9. Diagrame
cronopotentiometrice în 3% NaCl la 25°C (a) si
punctajul la testul feroxil (b) pentru otelul inoxidabil austenitic 7
(tab. 3.1) deformat prin refulare.
|
La otelul 8 (tabelul
3.1), cu un continut de
numai 6,22% Ni, spre deosebire de celelalte
oteluri studiate, potentialul electrochimic al sau se deplaseaza spre
valori pozitive în sensul
maririi stabilitatii la coroziune cu cât gradul de deformare este
mai
mare, figura 3.2.10a. La acest
otel si punctele Ms si Md asa cum rezulta din figura 3.1 se afla la
temperaturi superioare fata de
celelalte oteluri. Aceasta înseamna ca în timpul deformarii
plastice la
acest otel au loc
transformari structurale care duc la formarea martensitei α sau ε.
În
figura 3.2.10b este prezentat
testul cu solutie feroxil pentru acest otel.
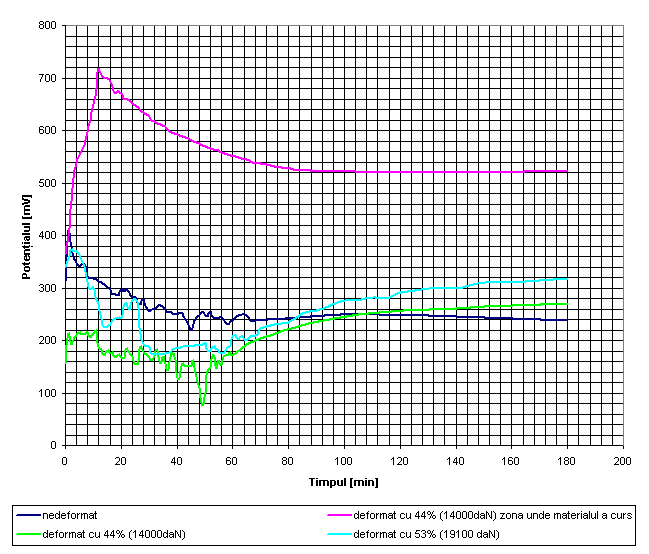
|
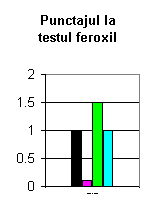
|
Figura 3.2.10. Diagrame
cronopotentiometrice în 3% NaCl la 25°C (a) si
punctajul la testul feroxil (b) pentru otelul inoxidabil austenitic 8
(tab. 3.1) deformat prin refulare.
|
Pentru otelul 9 (tabelul
3.1), cu un continut
de 8,75% Ni potentialul electrochimic al starii
deformate prin refulare cu 33% grad de deformare, se deplaseaza
nesemnificativ spre valori negative fata de a otelului nedeformat. Dupa
aproximativ 50 minute, otelul deformat are o
tendinta spre pasivare pâna la potentialul de 280-285mV, dar
revine în
scurt timp cam la aceeasi
valoare a potentialului otelului nedeformat.
|
|