
|
CAPITOLUL 1
|

|
Stadiul actual al cercetarilor privind
comportarea la
coroziune a otelurilor inoxidabile supuse deformarii plastice si
nitrurarii ionice.
|
1.1.
|
|
1.2.
|
|
1.3.
|
|
1.4.
|
|
1.2 Deformarea plastica la rece si
nitrurarea
otelurilor inoxidabile austenitice
Otelurile inoxidabile asa cum s-a aratat în figura 1.1.7
sunt foarte
utilizate în multe domeniide activitate. Un interes deosebit
prezinta
industriile chimica, alimentara si nucleara. Daca rezistenta lor la
coroziune este foarte buna, în schimb proprietatile tribologice
(rezistenta la uzura, coeficientul de frecare) si duritatea sunt
relativ
scazute. Din aceasta cauza trebuie evitat contactul între doua
oteluri
inoxidabile, pentru a evita distrugerea rapida a acestui cuplu.
Un rol important are deci alegerea optima a cuplului de
frecare
[178]. S-a constatat ca toate
cuplele de frecare primare (otel
inoxidabil pe otel inoxidabil), fara tratamente superftciale
sunt predispuse griparii, fara exceptie. Numai la regimurile usoare
gripajul poate sa nu apara. Cuplele de frecare secundare (suprafete
supuse tehnologiilor de ingineria suprafetelor) sunt sensibil mai bune
comparativ cu cuplele primare similare. In afara de a recurge la
materiale plastice dure, grafit sau bronzuri exista si posibilitatea de
a durifica superficial suprafetele de alunecare din oteluri
inoxidabile.
Astfel, se poate spune ca una din directiile de cercetare din
domeniul otelurilor inoxidabile este si aplicarea unor tehnologii de
ingineria suprafetelor care sa asigure duritate ridicata si proprietati
tribologice corespunzatoare conditiilor de solicitare si o pastrare sau
chiar o crestere a rezistentei la coroziune. Din studiul literaturii de
specialitate a rezultat un numar mare de tehnologii care urmaresc acest
deziderat. In figura 1.2.1 se prezinta principaleletehnologii de
ingineria suprafetelor aplicate otelurilor inoxidabile [179, 207,
83,
239, 12,169,124, 59, 120, 117, 156, 144, 125, 121, 102, 250, 104, 21,
146, 13]. In continuare se vor prezenta din aceste tehnologii doar
deformarea plastica la rece si nitrurarea.
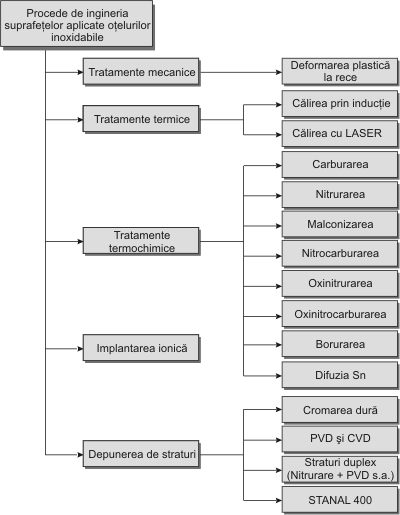
|
Figura 1.2.1. Tehnologii de
ingineria suprafetelor aplicate otelurilor inoxidabile [238, 227]. |
1.2.1. Deformarea plastica la rece.
Dupa TRUSCULESCU M. [220], pentru a stabili daca un otel
inoxidabil
sau refractar se preteaza sau nu sa fie prelucrat la rece prin
deformare
plastica trebuie sa se plece de la curbele de tractiune si
caracteristicile de ecruisare. Daca se considera figura 1.2.2 se
constata ca: otelurilemartensitice sunt putin ductile, au rezistenta
mecanica ridicata si ca atare sunt greu de prelucratla rece; otelurile
feritice au caracteristici de prelucrare la rece asemanatoare cu
otelurile carbon;otelurile austenitice prezinta o ductilitate ridicata
si se preteaza bine la prelucrarea la rece [218].
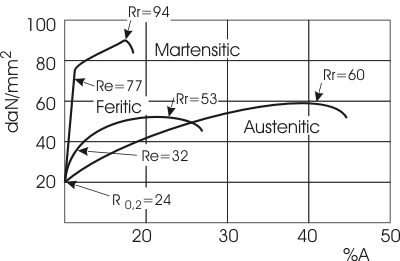
|
Figura 1.2.2. |
In timpul prelucrarii la rece apare fenomenul de
ecruisare,
care
poate fi favorabil sau nu prelucrarii. Coeficientul de ecruisare da
indicatii asupra ecruisarii si asupra aptitudinii oteluluide a fi
prelucrat la rece. Coeficientul de ecruisare n, se determina din
relatia [220]:
unde:
- σ - este tensiunea creata în material în
timpul deformarii;εl - este deformatia reala a materialului;
- l - distanta dintre doua repere ale epruvetei dupa
aplicarea
deformarii;
- l0 - distanta initiala dintre aceleasi
repere.
Otelurile inoxidabile austeniticeau n=0,4÷0,5
daca au
structura
stabila si 0,5÷0,95 daca structura este instabila. Gradul de
stabilitate
al austenitei se apreciaza prin coeficientul de stabilitate S [220].
S=ENi+2/5ECr;
ENi=30C+30N+0,5Mn+Ni;
ECr=Cr+Mo+Si.
Daca S≤22,5 austenita devine instabila - adica la
aplicarea
unor deformari poate fi transformata partial în structura de tip
martensitic si otelul se ecruiseaza.
Aprecierea capacitatii de a fi prelucrat la rece a unui
otel
austenitic se face, deci, luând în considerare valorile lui
n si S,
valori care trebuie sa fie între anumite limite pentru a nu
produceo
ecruisare prea puternica.
Dupa LACOMBE [129] în diagrama SCHAEFFER (figura
1.2.3)
se poate
observa ca otelulclasic 18/8 se afla la limita inferioara a domeniului
γ , în consecinta variatii mici ale elementelorα-gene sau γ-gene
pot
modifica structura austenitica.
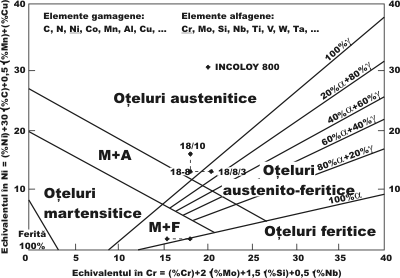
|
Figura 1.2.3. |
Din studiul literaturii de specialitate rezulta ca
pentru
durificare
prin tratamente mecanicea suprafelelor pieselor din oteluri inoxidabile
se pot aplica toate procedeele de deformare plasica superficiala
(durificarea prin rulare cu: bila, rola element toroidal, scula
vibratoare, durificarea prin lovire, soc laser, s.a.).
Dupa [176] exista patru tipuri de durificare prin rulare:
- durificarea prin rulare cu bila;
- durificarea prin rulare cu rola;
- durificarea prin rulare cu element toroidal;
- durificarea prin rulare cu scula vibratoare
(vibrorularea). Rularea de durificare este cunoscuta de mult timp. De
aproape o jumatate de secol au fost publicate lucrari asupra acestui
tratament mecanic de suprafata care duce la deformarea plastica a
straturilor superficiale si care s-a utilizat pentru cresterea
rezistentei la oboseala a pieselor cu zone de concentratori de tensiuni
(de exemplu razele de racordare a fusurilor si manetoanelor arborilor
cototi). Ca urmare a tensiunilor remanente de valoare ridicata
rezultate în urma rularii tensiunile de întindere sunt
suprimate, iar în
strat predomina tensiunile de compresiune. Eficacitatea rularii este
determinata de gradul de deformare. Durabilitatea cea mai mare a
pieselor în urma rularii se obtine la un anumit grad de
deformare.
Dupa
[39] exista un grad critic, care daca este depasit pot sa apara
fenomene
nedorite, ca de exemplu microfisuri si exfolieri ale stratului. De
asemenea s-a aratat ca exista o buna corelatie între duritatea
straturilor superficiale si limita de oboseala. Cresterea duritatii
duce
la cresterea limitei de oboseala. In figura 1.2.4 searata efectul
rularii asupra rezistentei la oboseala pentru un otel inoxidabil
austenitic.
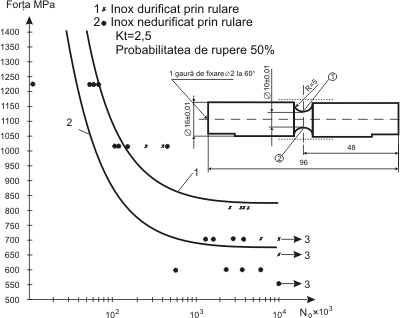
|
Figura 1.2.4. Influenta durificarii
prin rulare asupra rezistentei la oboseala a otelurilor inoxidabile
[33] |
În lucrarea [32] tensiunile remanente au fost
calculate
si apoi
masurate (metoda gaurii, metoda cu raze X), constatându-se o buna
corelatie între ele (figura 1.2.5).
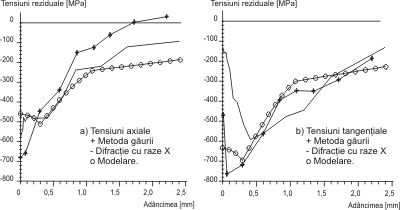
|
Figura 1.2.5 Tensiuni remanente
experimentale si calculate pe epruvetele netede [32]. |
In urma examinarii structurii obtinute dupa rulare
rezulta ca
s-au
format benzi de alunecaresi a aparut martensita (figurile 1.2.6 si
1.2.7). Din figuri rezulta ca rezistenta la oboseala de la 672MPa
pentru probele nedurificate prin rulare a crescut la 813 MPa pentru
probele durificate prin rulare, deci o crestere de 20%.
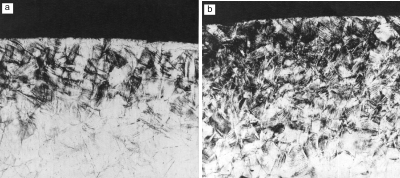
|
Figura 1.2.6. Formarea benzilor de
alunecare si aparitia martensitei (×50)[33]:
a) durificare prin rulare 3 min cu o forta de 20.000 N;
b) durificare prin rulare 3 min cu o forta de 40.000 N; |
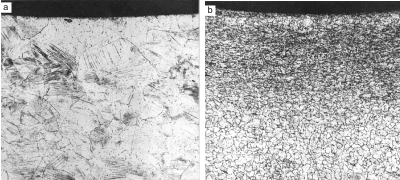
|
Figura 1.2.7. Formarea benzilor de
alunecare si aparitia martensitei [33]:
a) durificare prin rulare 1 min cu o forta de 9.500 N (×200);
b) durificare prin rulare 2 min cu o forta de 20.000 N (×100). |
În urma încercarilor experimentale [95, 176,
129,
7, 42] s-a
constatat ca rugozitatea suprafetelor si duritatea stratului
superficial
al piesei, de care depinde direct comportarea la uzura si aderenta,
depind de: calitatea si starea materialului piesei, geometria si starea
initiala asuprafetei piesei, geometria si dimensiunile elementului de
duricare si de cinematica procedeului de durificare prin deformare
plastica.
Rugozitatea initiala a piesei poate fi
îmbunatatita de 3
pâna la 40
de ori, iar duritatea poate sa creasca cu pâna la 100%, în
functie de
materialul piesei si de regimul de durificare.
În lucrarea [33] sunt prezentate unele rezultate
obtinute prin
rularea unui otel inoxidabil. Incercarile practice în acest caz
s-au
facut pe un otel inoxidabil austenitic cu 18%Cr, 12%Ni si 2%Mn,
ecruisat
la 600°C pentru a obtine caracteristici mecanice ridicate, în
special o
duritatede 320 HV30, Re=800MPa, Rm=900MPa.
În lucrarea [32] durificarea s-a facut pe o masina
fara
centre cu
doi galeti. Epruvetele au fostcilindrice cu dimensiunile de
∅45×50mm
rectificate. Galetii au avut diametrul de 142 mm. Timpul de tratament a
fost de 5 la 10 secunde. Efortul aplicat 4,8 si 16 tone.
In urma tratamentului s-a ameliorat calitatea
suprafetei.
Valorile
rugozitatii sunt prezentate în tabelul 1.2.2. Parametrii
rugozitatii nu
se modifica mult odata cu modificarea efortului si aduratei de
tratament.
Tabelul 1.2.2.Valorile
rugozitatilor obtinute dupa durificare prin rulare, cu alice si prin
ciocanire [33] |
Procedeul
dedurificare |
Ra,
µm |
Rp,
µm |
Rz,
µm |
Durificarea
prin rulare |
0,15 |
0,43 |
1,39 |
Durificare cu
alice(alicare) |
7,5 |
15,4 |
61 |
Durificarea
princiocanire |
9,1 |
14,2 |
50 |
|
Tensiunile remanente, masurate prin metoda
“gaurii” sunt prezentate în figurile 1.2.9 si1.2.10 [32, 33]. Din
analiza acestor diagrame rezulta ca efortul aplicat si durata de
tratament ducla dezvoltatea unor importante tensiuni remanente de
compresiune. In cele doua cazuri analizatetensiunea maxima este de
440MPa obtinuta în urma unui efort de 16t si a unei durate de
10s.Aceasta valoare este obtinuta la 0,25mm distanta de la suprafata
în
cazul tensiunilor axiale si la0,6mm pentru tensiunile tangentiale.
Adâncimea totala în care se afla tensiuni remanente este
de2mm.
Din punct de vedere mecanic, acest tratament mareste
rezistenta la
uzura a pieselor în frecare si îmbunatateste etanseitatea
asamblarilor,
în special când acestea sunt supuse la temperaturi
sipresiuni
importante. In figura 1.2.8 se prezinta variatia microduritatii
în
sectiunea probelor durificate prin rulare. In general duritatea creste
cu aproximativ 25%. Se poate atinge o valoare de 400HV la un efort de
16t. Duritatea galetului nu are importanta semnificativa asupra
duritatii otelului [32, 33].
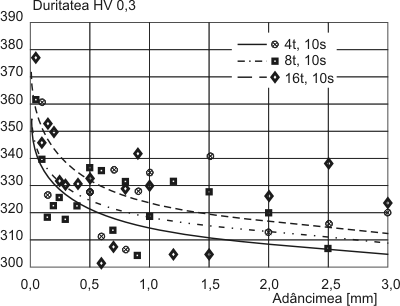
|
Figura 1.2.8. Efectul efortului
aplicat asupra duritatii [33] |
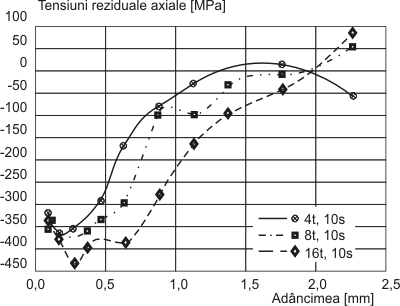
|
Figura 1.2.9. Efectul efortului
aplicat asupra tensiunilor reziduale axiale [33] |
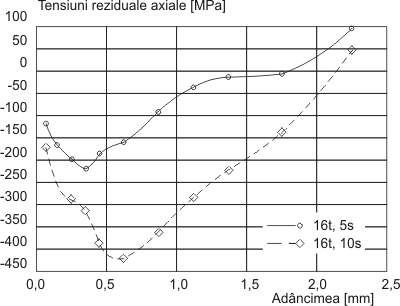
|
Figura 1.2.10. Efectul timpului de
tratament asupra tensiunilor reziduale circumferentiale [33] |
Rezultatele prezentate mai sus, obtinute în
conditii
industriale,
confirma datele din literatura. Durificarea prin rulare duce la
îmbunatatirea calitatii suprafetei, la cresterea duritatii si
la formarea în stratul superficial a unor tensiuni remanente de
compresiune. Efortul aplicat este parametrul primordial care asigura
introducerea tensiunilor remanente de compresiune.
Dupa anumiti autori [176, 177] reducerea razei de
curbura a
partii
active a galetului are influenta foarte mare asupra tensiunilor ca si
asupra ecruisarii stratului superficial. Acest aspect trebuie sa fie
înca cercetat si verificat. Nu s-au facut pâna în
prezent cercetari
legate de coroziune, de oboseala si de oboseala-coroziune si compararea
acestor rezultate cu alte tehnologii de ingineria suprafetelor.
In cazul durificarii prin rulare apar si unele
neajunsuri cum
ar fi:
micsorarea dimensiunilor, care este foarte diferita; aparitia pe
suprafata durificata a unor ondulatii ciclice; nu se recomandala
otelurile feritice de tipul 8TiCrl70 (exfolierea stratului superficial)
si la otelurile turnate(T15MoNiCr170) care datorita neomogenitatii
structurii ferito-martensitice si a incluziunilor de carburi metalice
dau o suprafata cu ondulatii foarte mari (macrorugozitate) si foarte
regulat distribuite.
Tehnologia de durificare a suprafetelor prin deformare
plastica este
o tehnologie ecologica [35, 233] si poate înlocui unele
tehnologii
poluante. Astfel în fabricatia decantoarelor centrifugale, la
arborii cu
flansa s-a înlocuit prin durificare cu bila, cromarea si
rectificarea suprafetelor cilindrice de etansare pentru masete de
rotatie. Tehnologia de durificare cu bila, pe lânga ca este de
cca
50 de
ori mai ieftina fata de cromarea dura + rectificarea suprafetei,
asigura o calitate si fiabilitate mai ridicate ale etansarii [152, 174].
1.2.2. Nitrurarea otelurilor inoxidabile
Aplicarea nitrurarii ofera multe avantaje: în
primul
rând datorita
temperaturilor scazute, deformatiile care apar sunt foarte reduse, ceea
ce confera o stabilitate dimensionala foarte mare. În al doilea
rând,
duritatea straturilor este foarte mare, ajungând la valori
pâna la
1000, 1200 HV [8, 151, 203, 36, 22, 208, 113].
Dintre procedeele de nitrurare, cele mai utilizate sunt
nitrurarea
ionica [105, 68, 14, 172, 11] si nitrurarea în gaz [171, 35, 159,
198,
233]. În ultimii ani s-au aplicat si o serie de variante
ale nitrurarii
cum ar fi: nitrocarburarea, oxinitrurarea, oxicarbonitrurarea si alte
procedee [243, 61].
La nitrurarea în gaz a otelurilor inoxidabile apar
unele
inconveniente legate de prezenta stratului pasiv, format din oxizi,
care
trebuie înlaturat înaintea nitrurarii. Pentru eliminarea
sau distrugerea
acestui strat pasiv s-au dezvoltat metode chimice, care maresc costul
tratamentului. Nitrurarea ionica a rezolvat acest aspect negativ,
deoarece în perioada de curatire când are loc fenomenul de
pulverizare
catodica acest strat pasiv este eliminat.
Principiile de baza ale nitrurarii ionice au fost
stabilite de
EDENHOFER, JONES si altii [78]. Cinetica reactiilor de nitrurare
cât si
fenomenele legate de pasivare au fost studiate de maimulti cercetatori
[66, 123, 185, 97, 150, 148], iar fenomenele legate de efectul catodic
suntstudiate în lucrarile [97, 43, 96, 18].
Cele mai multe lucrari de cercetare au pus accentul pe
întelegerea
fenomenelor metalurgice care apar la nitrurarea ionica, pe formarea
stratului de compusi si a stratului de difuzie [66, 48, 194, 214, 166,
54, 53, 103, 205]. Stratul de compusi format într-o atmosfera
fara
hidrocarburi în cazul nitrurarii ionice este γ́ asa cum rezulta
din
sistemul Fe-N.
Un rol important în procesul de nitrurare îl
are
temperatura [187,
136, 69, 70, 31]. La temperaturi joase de nitrurare (de exemplu la
350°C) atomii de substitutie ai fierului (Cr, Ni, s.a.) au o
mobilitate
mai mica, dar datorita faptului ca modifica coeficientii de activitate
ai azotului în fier, poate avea loc o intensificare a
precipitarii
nitrurii de fier din solutia solida suprasaturata. Din cercetarile
efectuate de EDENHOFER [78] s-a desprins idea ca nitrurarea ionica
la temperaturi joase este posibila urmând un mecanism special.
Unele
elemente de pe suprafata otelului inoxidabil sunt pulverizate în
spatiul
incintei de nitrurare, chiar la temperaturi joase,combinându-se
cu
azotul si ducând la formarea de nitruri.
Un dezavantaj major a otelurilor inoxidabile nitrurate
este
scaderea
rezistentei la coroziune. Aceasta scadere a rezistentei la coroziune se
datoreaza reducerii continutului de crom [85]. În acest sens s-au
facut
încercari de a utiliza un tratament de oxidare dupa nitrurare,
în
aceleasi conditii cu nitrurarea ionica, pentru a reconstitui stratul
pasiv, prin aceasta ar trebui sa se îmbunatateasca rezistenta la
coroziune. Încercarile de refacere a stratului de oxizi pentru
a îmbunatati rezistenta la coroziune dupa nitrocarburare au fost
facute
de mai multi cercetatori [195, 193, 39].
DEARNLEY s.a. [66, 55, 249, 44, 86, 119, 186, 126, 23,
63,
143] au
aratat ca nitrurarea ionica a otelurilor inoxidabile poate fi o solutie
de viitor pentru a mari proprietatile tribologice fara sa fie afectata
rezistenta lor la coroziune. În timpul nitrurarii ionice au loc
schimbari importante ale structurii straturilor superficiale
determinate
de temperatura. La temperaturi de nitrurare cuprinse între
450-600°C în
straturile superficiale apar nitruri de crom care conduc la diminuarea
puternica a rezistentei la coroziune. Dupa [257] temperatura de
nitrurare trebuie sa fie situata între 400-500°C, iar dupa
altii [79]
între 350-420°C si chiar între 250-450°C [66].
ZHANG si BELL [257] se pare ca au pus în evidenta,
pentru prima
data, formarea unui strat cu duritate ridicata si cu o buna rezistenta
la coroziune. Acest strat dupa EL-HOSSARY [79] este faza “S” aceeasi
denumire fiind data si de ICHII si colaboratorii [112]. Dupa alti
cercetatori, stratul este format dintr-o solutie solida de azot
în
austenita otelului inoxidabil, solutie solida suprasaturata [85, 185].
Nitrurarea în plasma a patru calitati de oteluri
inoxidabile
(tabelul 1.2.3) în aceleasi conditii de tratament au aratat
faptul
ca
Fe, Cr si Ni sunt absolut necesare pentru formarea fazei “S”. Otelurile
continând numai 13% Cr sau 42% Ni nu formeaza faza “S”, în
schimb la
otelul duplex (austenito-feritic) dupa nitrurare stratul superficial
este format în majoritate din faza “S”. Analiza unui strat de la
suprafata de grosime 50nm din otel 304L nitrurat la 450°C a ratat
ca
azotul ajunge pâna la 23,5-26,5% (tabelul 1.2.4), cromul,
nichelul
si
fierul având unele abateri fata de materialul de baza.
Tabelul 1.2.3. Compozitia
chimica a otelurilor utilizate [18]. |
Marca |
Compozitia
chimica,
% |
Cr |
Ni |
Mn |
Si |
C |
P |
Mo |
Fe |
AISI
304 |
18,04 |
10,13 |
1,48 |
0,37 |
0,025 |
0,026 |
-
|
rest |
1.4021 |
13,0 |
-
|
< 1
|
< 1
|
0,2
|
-
|
-
|
rest
|
1.4460
duplex |
26,7
|
4,5
|
< 2
|
< 1
|
0,1
|
-
|
1,5
|
rest
|
1.3917 |
0,01
|
42,1
|
0,9
|
0,1
|
0,04
|
-
|
-
|
rest
|
|
Tabelul 1.2.4. Compozitia chimica a
fazei S [18] |
Element
|
Continut
%
|
XPS
|
EDX
|
Fe(4)
|
49,0
|
48,9
|
Cr(1)
|
14,5
|
14,8
|
Ni(1)
|
13,0
|
9,8
|
N(2)
|
23,5
|
26,5
|
|
Dupa [183, 176, 182, 153, 140, 190, 122, 24, 87, 141],
nitrurarea
otelurilor inoxidabile este un fenomen complex si insuficient studiat,
care conduce la morfologii de straturi foarte diferite influentate
puternic de temperatura si de potentialul de azot. Daca nitrurarea se
face la temperaturi inferioare celei de 650°C se obtine un strat
foarte
dur (1600 HV în cazul otelului 18-10).
În acest domeniu de temperatura, ca urmare a
diminuarii
energiei
defectelor de împachetare are loc o destabilizare a austenitei,
cu
formarea unei faze feritice prin mecanismul de germinare si
crestere. Cinetica cresterii stratului este controlata prin difuzia
azotului în ferita.
La temperaturi de nitrurare mai mari de 650°C
austenita
este stabila
si nu mai sunt zone de transformare γ→γ+α. Prin difuzia azotului
în
austenita se limiteaza posibilitatea cresterii stratului. Prezenta
feritei se datoreaza saracirii în crom a matricei ca urmare a
precipitarii nitrurii de crom Cr2N. Cauza aparitiei feritei
se datoreaza deci altor aspecte decât cele observate la
temperaturi mai joase.
Aceste rezultate arata ca este putin previzibila o
oarecare
ameliorare a rezistentei la coroziune a straturilor nitrurate ale
otelurilor inoxidabile. Dupa [20, 94] numai un strat superficial de
nitruri foarte stabile permite cresterea rezistentei la coroziune. Se
poate realiza si o nitrura TiNcare sa confere materialului proprietati
excelente la coroziune [204, 225].
O alta grupa de cercetari, desprinsa din studiul
literaturii
de
specialitate [2094, 21183, 2452, 25196,4771, 13671, 224, 160, 47, 30,
50, 40, 240, 242], s-a referit la influenta diferitelor tehnologii de
nitrurare asupra rezistentei la coroziune si a proprietatilor
tribologice. În acest sens s-au luat în
considerare urmatoarele
tehnologii: nitrurarea în gaz, nitrurarea în plasma,
nitrocarburarea în
bai de saruri, cu si fara tratament ulterior de oxidare.
Încercarile
s-au facut pe oteluri inoxidabile austenitice marcile AISI 304, AISI
316
si AISI 321. Nitrurarea în gaz s-a realizat la 540°C timp de
45 h
într-un cuptor de tip clopot. Nitrocarburarea în bai de
saruri dupa
procedeul TF1-TUFTRIDE, s-a efectuat la 580°C, timp de 90 minute,
urmata
de o racire rapida într-o baie AB1, la 370°C cu o mentinere
de
20 minute
si apoi o operatie de spalare în apa curenta. Mentionam ca
probele supuse nitrocarburarii au fost în prealabil
preâncalzite la
350°C. Nitrurarea în plasma, cu parametrii trecuti în
tabelul 1.2.5 s-a
facut într-o instalatie de nitrurare în plasma de 10kW.
Tabelul 1.2.5. Parametrii
nitrurarii ionice [183]. |
Tratamentul |
Temperatura
[°C] |
Timp
[h] |
Vidul
initial[mbar] |
Numarul
depurjari
ciclice |
Pulverizare cu H2
Nitrurare ionica |
380
380
|
2
48
|
> 10-1
|
5
|
Pulverizare cu H2
Nitrurare ionica |
460
460
|
2
20 |
>10-1 |
5 |
Pulverizare cu H2
Nitrurare ionica
Oxidare |
460
460
460
|
2
20
20 |
>10-1 |
5 |
|
Oxidarea ulterioara s-a realizat prin introducerea de
oxigen
(“uscat” fara vapori de apa) timp foarte scurt. Înainte de
introducerea
oxigenului s-a întrerupt alimentarea incintei cu hidrogen si
azot.
Dupa
20 de secunde cât a durat introducerea oxigenului, în
incinta s-a
introdus din nou amestecul de azot si hidrogen pentru accelerarea
racirii. Aspectul suprafetelor probelor supuse acestor tratamente a
fost
diferit. La probele nitrurate în gaz suprafata a avut o culoare
gri
închis. La probele nitrocarburate în baie de sare
suprafetele au fost
negre datorita filmului de oxizi format în timpul mentinerii
în baia AB1
(oxidare).
Probele nitrurate în plasma la 460°C au o
culoare
gri închis, iar
cele nitrurate la 380°C sunt de culoare gri deschis. Toate probele
supuse oxidarii dupa nitrurare, au o culoare albastruie, indicând
prezenta unui strat subtire de oxizi. Studiul metalografic a aratat ca,
dupa nitrurare straturile de la suprafata difera mult în
functiede
calitatea otelului. La otelul AISI 316 se pot distinge trei zone I, II,
III. Aceste zone au fost confirmate si de alti cercetatori [997].
În
zona I s-a observat γ́+austenita; în zona II structura se compune
din
austenita, ferita si nitruri de crom; iar în zona III se constata
numai
austenita suprasaturata în azot. La otelul AISI 304 cele trei
zone
ale
stratului nitrurat nu sunt la fel ca la otelul AISI 316. În cazul
otelului AISI 321 nu se observa prezenta zonei I (figura 1.2.11)
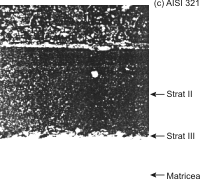
|
Figura 1.2.11. Microstructuri ale
otelurilor inoxidabile austenitice nitrurate ionic.
a) AISI 304L (×450); b) AISI 316L (×450); c) AISI 321L
(×490).
Atac cu NITAL 5% a si c, atac electrolitic cu 10% acid oxalic b
[183]. |
Probele nitrocarburate în bai de saruri au
structuri
asemanatoare cu
cele obtinute prin nitrurare în plasma, dar grosimea
strarturilor acestora în cazul otelului AISI 321 este mai mica.
Structurile obtinute dupa nitrurarea în gaz pentru AISI 304 si
AISI 316
nu sunt uniforme, iar pentru otelul AISI 321 nu se pot disteinge cele
trei zone.
În tabelul 1.2.6 se arata grosimea diferitelor
straturi
obtinute
dupa nitrurare la temperaturi joase (250 - 450°C) si la temperaturi
înalte (500 - 600°C). Pentru fiecare din cele doua
oteluri studiate se
deosebesc tei straturi fixe: un strat alb continând ace de
nitruri
(C1), un strat gri (C2) si un strat alb (C3), sau doua straturi
succesive, din care un strat gri de grosime mare (C0) si un strat alb
nitrurat (C1).
Tabelul 1.2.6. Grosimea straturilor
nitrurate la oteluri inoxidabile [223]. |
|
Nitrurare
ionica la
|
temperaturi
joase
|
temperaturi
inalte
|
Marca
otel
|
304L
|
316L
|
304L
|
316L
|
Grosimea C0,
µm |
-
|
-
|
10
|
28
|
Grosimea C1,
µm |
4
|
1,5
|
-
|
2
|
Grosimea C2,
µm |
1
|
2
|
-
|
-
|
Grosimea C3,
µm
|
1
|
1
|
-
|
-
|
|
|